The other day I hauled the transmission, electric motor and chunk of aluminum to work, where the mating of the motor and transmission will take place. The transmission was absolutely filthy from an engine oil leak and took a good 15 minutes of steam cleaning to get it spotless.
Today I started work on adapting everything together. First off, I am mating the transmission to the keyed shaft side of the motor. Originally this motor was coupled on the opposite end where there is still a gear on the end of the shaft. Unfortunately, the opposite end (the end I want to couple to) has only three 5/16" threaded holes to mount the motor. You can see the three tiny holes around the edge of the motor face.
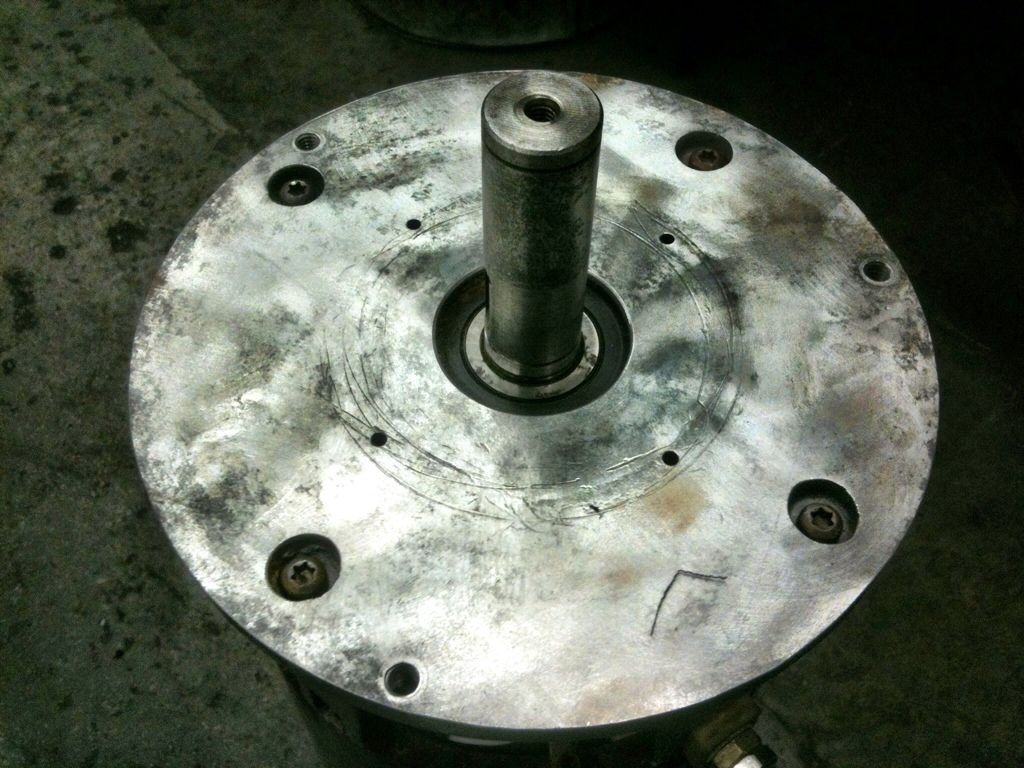
Not strong enough. I usually prefer overkill. So today I performed some precise measurements and drilled three 21/64" holes into [what I figured was] the thickest part of the face approximately 5/8" deep. Turns out I was right, as I did not go through the motor face anywhere (and get aluminum filings inside the motor). I tapped the holes 10mmX1.5 and made up three short studs.

Studs are the strongest when torquing into aluminum. I will Loctite the studs into the motor face and torque it up to the adapter plate with nuts. Metal on metal instead of torquing into aluminum.