Classic cedar strip construction can easily achieve a smooth, sexy shape for a bed cover. While canoe, kayak and other small boat builders typically use Western Red Cedar for the base material, that is based mostly on its relative lightness and easy workability with hand and power tools due its subdued grain structure. As a bonus, western red cedar ranges in color from almost white to deep maroon and brown offering the opportunity to create custom artistic effects in the hull.
Overall weight won't be a major issue in a bed cover however, and use of any relatively knot-free soft wood should do. (Knots up to the diameter of a pencil eraser while unsightly are acceptable so long as they are not at an edge.) Fir, while acceptable, can be a real PITA due its strong grain stricture. When shaping the edges of the strips, long, thin needle-sharp splinters are easily created. These are painful at least, and when broken off can affect, the strength of strip-to-strip joints. Other softwood such as pine, spruce, hemlock -- even poplar, cypress and redwood when weight is not a major consideration and the structure will be painted -- are greatly easier to work.
Most often the individual strips are made with a "cove and bead" treatment on opposite long edges; one side curves outward, the other inward. This creates sort of a modified ball and socket-like mating surfaces. This method allows adjacent strips to be pulled tightly together going around curves for maximum glue effectiveness making for tight, strong glued up. As a secondary effect the tightness prevents "show through," light shining through thin strips of cured glue between strips in the finished hull… a sure sign of an amateur, first time building effort… but not really a strength issue if they are small and far spaced apart.
If you are really handy with a razor sharp, low angle block plane you can plane rolling. constantly changing bevels on the edges of adjacent strips so that they fit tightly together alone their full length. But this is usually the province of really experienced builders.
It is not necessary for every strip to run the full length of the structure. Typically end-to-end butt joints for the strips are acceptable if they occur one in every three strip runs and are widely spaced apart. This feature is often use to make mosaic-like artistic designs -- of even birds, fish, etc. -- in some hulls.
Coating the structure with the epoxy/'glass on the outer surface of a bed cover will be relatively easy due its convex curvature. On the inside concave surface the 'glass tends to pull away from the surface but this tendency can be over with patience and practice. Any unsightliness will not be apparent from the outside.
The cedar strip construction is covered with epoxy and fiberglass cloth which gives it the vast majority of its strength and puncture resistance. But epoxy left by itself in the sun suffers from gradual degradation due exposure to harmful ultraviolet light. This can be overcome by coating with multiple coats of a high quality varnish with UV blocker. For a structure essentially exposed to full sunlight everyday, that would be 8-10 thick coats at initial build, and at least four coats reapplied each year as the varnish gradually, imperceptibly ablates -- is burned off by the sun. On a bed cover, varnishing would be more a matter of ego than practicality. Might as well paint the structure for low maintenance.
I recommend that you visit some cedar strip building sites on the Inter-web, there are lots of them. Stay away from obvious slash and cut, quick and dirty presentations. When it comes to buying a book, Ted Moore's
Canoecraft is the acknowledged bible.
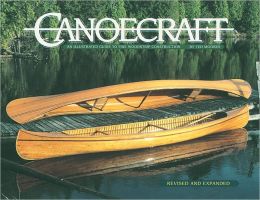