Quote:
Originally Posted by oil pan 4
At home I use a crimper the size of a large lock cutter with rotating dies that crimps everything from 6 gauge to 3/0 gauge.
The crimper crimps ring terminals down on welding cables that will be used in high vibration and will be getting flexed and pretty much everything else.
Also works great on SB175 connectors.
I usually just crimp them in the middle so there is a smooth transition between flexible cable and the crimp, because I found when they are crimped all the way to the end of the lug strands break like crazy.
Plus I need something a little more portable than a shop press.
|
I have a variety of bolt cutter style crimpers, but I always measure higher resistance with those crimps. I tests my connections at 700 amps, and between 100 and 120 volts DC, and this seems to be where resistance variances between my batteries show up the most if the connections are not perfect. I have a real time display of all of my high current circuit connections in my pack that I can watch and record as I drive, that shows resistance and voltage of each connection. When I drive around normally, "good" connections read fine, but when I get up into the 500 to 700 amp range, I can see variances in resistance between each battery. My display has each battery numbered, so I can go right to my highest resistance connection without having to look at all the others. I cut them open, and study them, and then improve on them.
The broken strand thing that you mention is spot on, and I have had to shape my anvils many different ways to make a crimp that is "nice" to all the strands. The edge of the anvil has to be tapered so that it does not cut into the lug and the strands on the other side of the stress point. Here is a proper crimp, view of the non stressed side:
Here is a view of that same crimp on the stressed side. Notice the 45 degree cross taper. This is so that I don't shear the strands:
I do a cross cut after I chop the connection in half, and this allows me to study the stress point of the strands. I had to make a lot of anvils to finally get where I don't break any strands. You can see some damaged strands where I chopped it in half, but those are from my cutter.
I also like to go portable with my crimpers, so I have built one that I can use my 1/2" impact wrench on. I wish I could bring my shop press with me sometimes, but this crimper will do the job when I can't bring it. My shop press crimper does not have those big bolts on the ends like this one does.
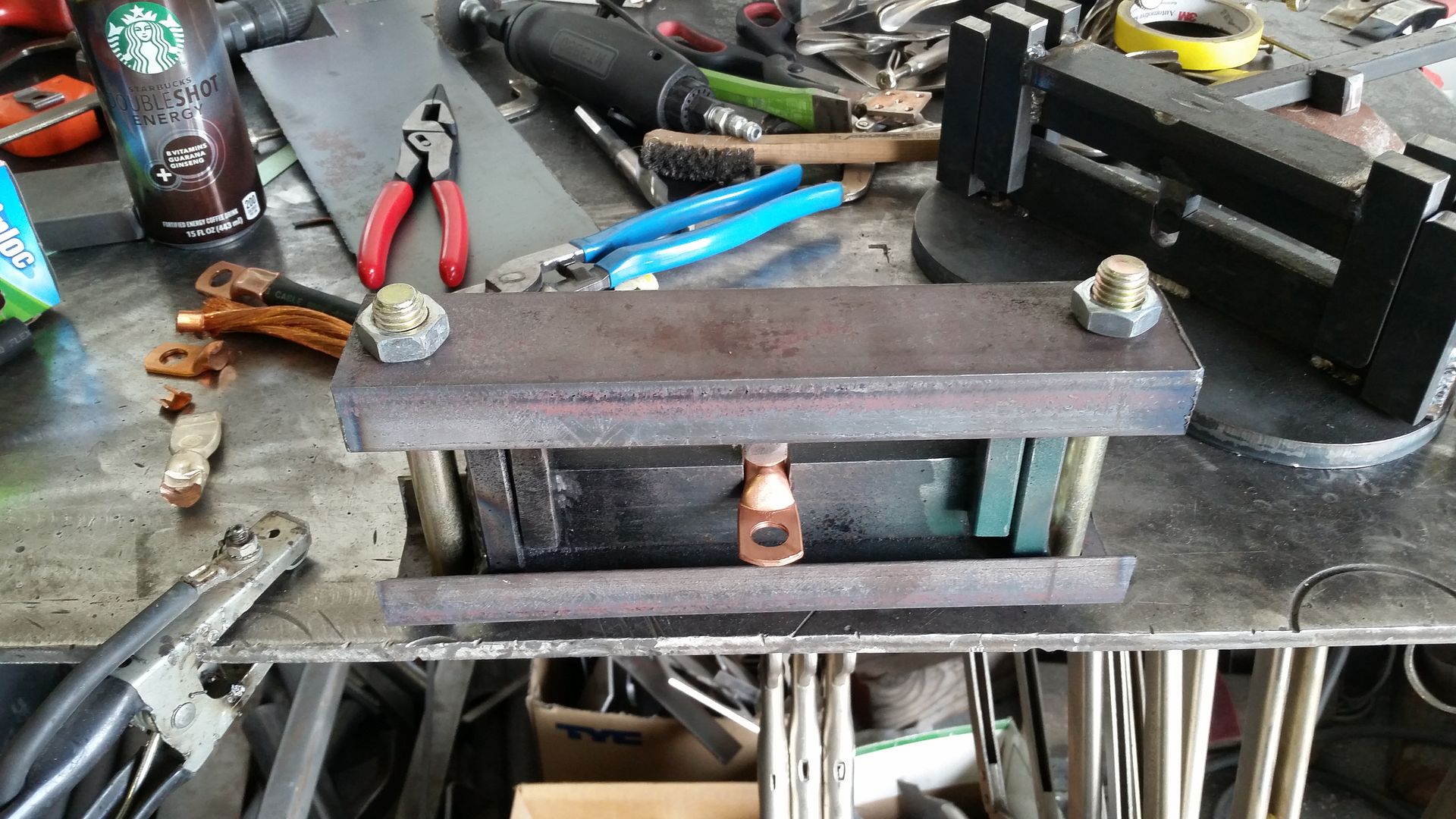