05-29-2012, 10:19 AM
|
#91 (permalink)
|
Master EcoModder
Join Date: Jul 2011
Location: Ann Arbor, Michigan
Posts: 4,179
Thanks: 127
Thanked 2,802 Times in 1,968 Posts
|
__________________
George
Architect, Artist and Designer of Objects
2012 Infiniti G37X Coupe
1977 Porsche 911s Targa
1998 Chevy S-10 Pick-Up truck
1989 Scat II HP Hovercraft
You cannot sell aerodynamics in a can............
Last edited by kach22i; 05-29-2012 at 10:25 AM..
|
|
|
Today
|
|
|
Other popular topics in this forum...
|
|
|
05-29-2012, 10:32 AM
|
#92 (permalink)
|
Master EcoModder
Join Date: May 2008
Location: Maynard, MA Eaarth
Posts: 7,907
Thanks: 3,475
Thanked 2,950 Times in 1,844 Posts
|
Narrowing the rear wheel track to be able to taper the rear fenders in plan would help lower the drag quite a bit -- by up to 40-45%. Your Mk 10.2 (and 10.3?) appear to have this. But the sides need to taper smoothly, and not "re-expand" around the rear wheels.
If you widen the front of the cabin slightly, the rear passenger could gain some much needed legroom; by letting their feet rest between the front seats. They have to be able to climb in to the rear seat, so this space would be well worth having.
The other point of reference on the Illuminati 'Seven' is their solution for gaining rear headroom for the rear is to have the rear passengers face backward.
|
|
|
05-29-2012, 12:25 PM
|
#93 (permalink)
|
Master EcoModder
Join Date: Jul 2011
Location: Ann Arbor, Michigan
Posts: 4,179
Thanks: 127
Thanked 2,802 Times in 1,968 Posts
|
Quote:
Originally Posted by NeilBlanchard
1. Narrowing the rear wheel track
2. If you widen the front of the cabin slightly, the rear passenger could gain some much needed legroom; by letting their feet rest between the front seats.
3. ..................rear passengers face backward.
|
Thanks for the continued discussion Neil.
1. I don't want to narrow the rear track, or make it a 3-wheeler. For this exercise I want to solve for a simple four corner car, maybe I'll do as you mention on a future exercise. I'm setting some self imposed limits for no reason other than setting some restrictions to solve by. For instance, I don't want van/truck-like upright seating and therefore want to keep this exercise low like a car.
2. I think the layout you suggest combined with the bubble front I have would lead to a four diamond in lieu of four square seating pattern. However, with this car so cab-forward already I would not dare make it any wider.
3. I looked at rear facing rear seating before on the VW Beetle thread. In that situation it did not work well because of that engine, but I also did not see a huge advantage either (admit to small advantage).
I want to keep with the three seating layout as I did with the plastic poster board model which used gold balls as helmets.
Three seats is something already in the market in my opinion. Any 2+2 such as a Porsche 911 with tiny rear seats, allows an adult to sit sideways, or at least toss one leg over to the other side of the center hump.
Old VW thread mentioned:
http://ecomodder.com/forum/showthrea...-16550-18.html
EDIT: 06/01/12 UPDATE
Industrial Design - Transportation pictures by kach22i - Photobucket
EDIT-UPDATE 06/02/12
Industrial Design - Transportation pictures by kach22i - Photobucket
EDIT 06/03/12 Added a side vent similar to the earlier sketch
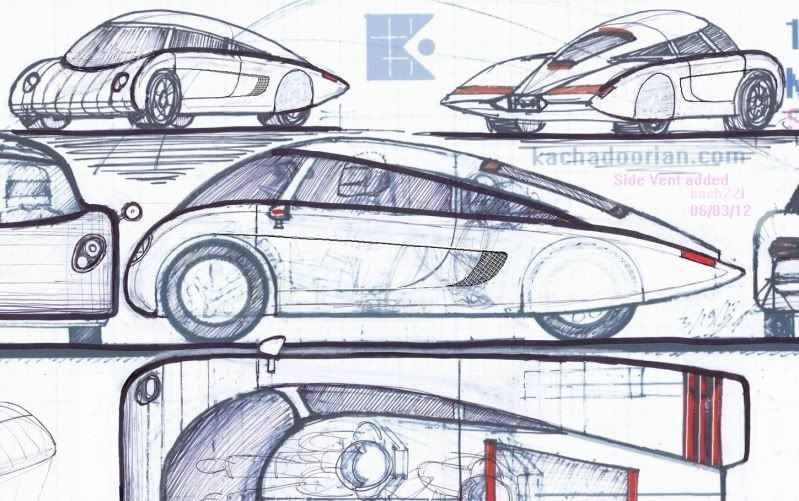
Like this one:
More Changes:....headlights
Even more 06/04/12
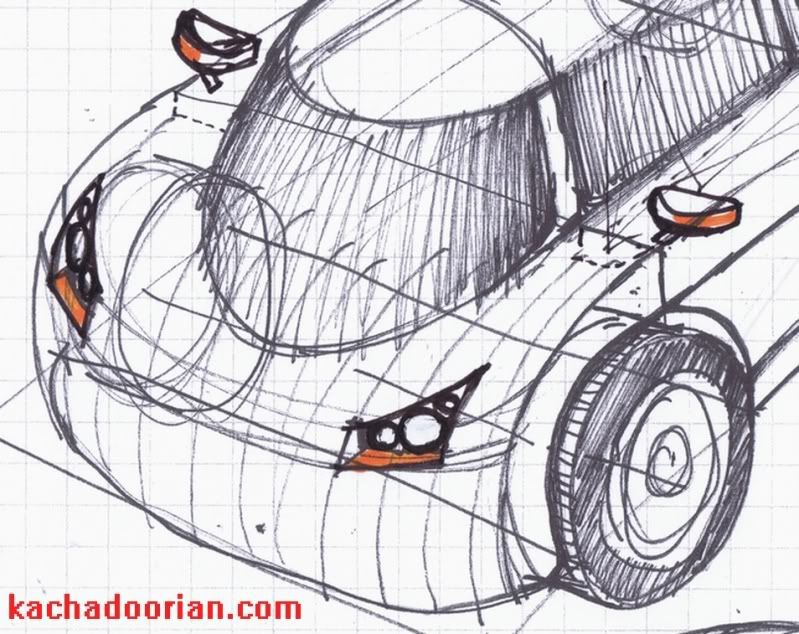
__________________
George
Architect, Artist and Designer of Objects
2012 Infiniti G37X Coupe
1977 Porsche 911s Targa
1998 Chevy S-10 Pick-Up truck
1989 Scat II HP Hovercraft
You cannot sell aerodynamics in a can............
Last edited by kach22i; 06-04-2012 at 10:35 AM..
|
|
|
02-26-2013, 03:53 PM
|
#94 (permalink)
|
Master EcoModder
Join Date: Jul 2011
Location: Ann Arbor, Michigan
Posts: 4,179
Thanks: 127
Thanked 2,802 Times in 1,968 Posts
|
UPDATE: 02/26/13
I'm still not working in clay or foam yet, still playing with sketches once in a while.
Industrial Design - Transportation Photos by kach22i | Photobucket
This design gets the feet back, and narrows the rear track quite a bit.
Better results all around, maybe not a "pure" as some of my other attempts, but more practical to be sure.
__________________
George
Architect, Artist and Designer of Objects
2012 Infiniti G37X Coupe
1977 Porsche 911s Targa
1998 Chevy S-10 Pick-Up truck
1989 Scat II HP Hovercraft
You cannot sell aerodynamics in a can............
|
|
|
The Following 2 Users Say Thank You to kach22i For This Useful Post:
|
|
03-11-2013, 02:49 AM
|
#95 (permalink)
|
EcoModding Lurker
Join Date: Nov 2011
Location: United States
Posts: 82
Thanks: 18
Thanked 7 Times in 6 Posts
|
Quote:
Originally Posted by kach22i
Think less marketing, and more about forum.
The attraction of building a car in the same manner I would a hovercraft, with Monopan is an important part of this concept. It is just not as important at the model stage.
MonoPan :: The Future in Material Technology
Curving glass would not be so simple, but the windshield is just a slice of a cone in this design.
This would be a car for myself, screw what anybody else wants, I'm creating art here. 
|
I like the simplicity,I would like to see you reduce the frontal area,why not narrow the car ,like the XL1,you end up with less overall weight,better aerodynamics,how about fans in the rear, verse's extending and tapering the body work?would it work?is it worth the extra hardware,electrical load,etc?We all bring something to the table,too bad we all weren't in a shop together,building a open source commuter vehicle,200 plus mpg,turbo diesel,electric,that also is comfortable,has good ergonomics,really good looking.Driving to LA to NY on 50 dollars plus,yes. 
|
|
|
03-11-2013, 03:56 AM
|
#96 (permalink)
|
Master EcoModder
Join Date: Aug 2012
Location: northwest of normal
Posts: 28,557
Thanks: 8,092
Thanked 8,882 Times in 7,329 Posts
|
There're about three paragraphs of content in that run-on. 'Verses'?
I like Monopan. Other composite materials are available, like PlyMetal Swing Door, 5/8" plywood with aluminum skins, or PlyMetal Plus Swing Door with aluminum on one side and HDPE plastic on the other.
Autospeed - Cardboard Cars? has a good discussion of similar materials used in University of South Australia’s ‘Trev’ (aluminum core with FRP skins), before moving on to cardboard.
Quote:
how about fans in the rear, verse's extending and tapering the body work?would it work?is it worth the extra hardware,electrical load,etc
|
No.
|
|
|
03-11-2013, 10:20 AM
|
#97 (permalink)
|
Master EcoModder
Join Date: Jul 2011
Location: Ann Arbor, Michigan
Posts: 4,179
Thanks: 127
Thanked 2,802 Times in 1,968 Posts
|
Quote:
Originally Posted by freebeard
Other composite materials are available, like..........
|
Nice links, but making compound curves looks difficult, lot of steam bending or at least soaking involved.
I've gotten away from the flat plane concept I started with, although I just know one day I'll return to it for another study.
My latest sketches are much more complex and would require 3Tex/Zplex, molds and vacuum bagging.
Homepage:
3TEX Incorporated | 3TEX, Inc.
Z-Plex
ZPlex - Total Conformable Sandwich System | 3TEX, Inc.
Quote:
The 100s of slender flexible foam cores move freely like the yarns, providing a deeply conformable structure...................
Applications; Curved parts difficult to make with balsa or rigid foams
Lightly loaded parts like car hoods, ducts, engine covers, doors.....
|
Maybe I can blend different technologies and materials. For instance; start with a very light gauge and bendable conduit (plastic or metal), cover with a single plane bendable product (Monopan?), and for the complex and compound curves found at the front, back and corner/plane intersections use fiberglass over hand sanded foam or Z-Plex pieces.
The very light gauge and bendable conduit (plastic or metal) used as the mounting framework for body shell construction, could be used to run wires or later filled with structural foam.
__________________
George
Architect, Artist and Designer of Objects
2012 Infiniti G37X Coupe
1977 Porsche 911s Targa
1998 Chevy S-10 Pick-Up truck
1989 Scat II HP Hovercraft
You cannot sell aerodynamics in a can............
Last edited by kach22i; 03-11-2013 at 10:34 AM..
|
|
|
03-11-2013, 02:41 PM
|
#98 (permalink)
|
Master EcoModder
Join Date: Aug 2012
Location: northwest of normal
Posts: 28,557
Thanks: 8,092
Thanked 8,882 Times in 7,329 Posts
|
Quote:
Nice links, but making compound curves looks difficult, lot of steam bending or at least soaking involved.
|
I don't think steaming or soaking is going to work with some of these materials. But cardboard—definitely. I bookmarked the Z-Plex page. Too bad they only recommend it for non-structural uses.
Quote:
Maybe I can blend different technologies and materials. For instance; start with a very light gauge and bendable conduit (plastic or metal), cover with a single plane bendable product (Monopan?), and for the complex and compound curves found at the front, back and corner/plane intersections use fiberglass over hand sanded foam or Z-Plex pieces.
|
That's what the Trev folk did. http://www.trevipedia.net/index.php?title=Main_Page
I've been experimenting with Polymetal. I've run it through a sheet metal roller/brake/shear to assess it for the final build of a boattail.
Here's what's essentially aluminum skinned coroplast. AlumaCorr
|
|
|
03-12-2013, 11:07 AM
|
#99 (permalink)
|
Master EcoModder
Join Date: Jul 2011
Location: Ann Arbor, Michigan
Posts: 4,179
Thanks: 127
Thanked 2,802 Times in 1,968 Posts
|
Quote:
Originally Posted by freebeard
|
I followed the tub link to here:
United States Panel Range
I still like Monopan better as the skin is the same plastic material as the core, plus a layer of fiberglass.
The Trev is a lot of expandable foam over a honeycomb tub, right? I like that approach because the foam offers energy absorption with light weight, at least until the foam absorbs moisture out of the air, then it could gain a few pounds.
Quote:
Originally Posted by freebeard
I've been experimenting with Polymetal. I've run it through a sheet metal roller/brake/shear to assess it for the final build of a boattail.
|
Followed the link to here:
http://nudo.com/Spec-Sheet/Default.aspx
I cannot get any of the PDF's to open.
__________________
George
Architect, Artist and Designer of Objects
2012 Infiniti G37X Coupe
1977 Porsche 911s Targa
1998 Chevy S-10 Pick-Up truck
1989 Scat II HP Hovercraft
You cannot sell aerodynamics in a can............
|
|
|
03-12-2013, 02:45 PM
|
#100 (permalink)
|
Master EcoModder
Join Date: Aug 2012
Location: northwest of normal
Posts: 28,557
Thanks: 8,092
Thanked 8,882 Times in 7,329 Posts
|
Quote:
The Trev is a lot of expandable foam over a honeycomb tub, right? I like that approach because the foam offers energy absorption with light weight, at least until the foam absorbs moisture out of the air, then it could gain a few pounds.
|
My biggest concern with their method is the formers that guided the shaping of the foam, which appear to extend to the fibergkass skin. One of the people building a aerocap for his pickup here had problems with ripples showing up in his fiberglass work:
Quote:
Originally Posted by a8ksh4
I've had the side panels on the truck for a couple weeks now, putting them through some temperature cycles from below freezing in the mornings to 70s in the afternoon as well as some rain and frost. When they were new, the surface was nearly mirror smooth, but they're starting to ripple a bit on the surface. There is a bit of a raised line on one where the glass crosses a joint in the foam underneath.
|
Quote:
I cannot get any of the PDF's to open.
|
Nor I. It looks like their page is broken.
|
|
|
|