Mwa ha ha ah ha ha ha!
Got some more work done!
I drilled holes in the bottom corners of the cover and put T-nuts in them. They will act as a hole for the prop-rod to go in AND I can thread in eye-bolts to make safety tie-down points as needed.
I glue-coated and then fiberglassed the TOP of the cover.
I took off my last disposable rubber glove to answer the phone in the middle of a resin pour before realizing it was the last of my rubber gloves. Good thing there was a box of Ziplock bags handy. I finished the fiberglassing with one hand in a Ziplock mitten.
The big news is that I got a call back from "Hot Rod" Jim, who helped me with the adapter plate and original LoveJoy coupler on the Electro-Metro project.
I had been wanting to talk with him about my whole "Super-Truck" idea and specifically meet with him about details of connecting the electric motor, transmission, and shortened drive shaft.
I learned plenty just by chit-chatting with him for a bit. He had a number of drive-shafts in the back of his shop and showed how easy it is to use a lathe to chop, shorten, or balance driveshafts.
The current plan is to use a solid coupler (very similar to what was used as the second coupler in the Metro) to attach the output of the tranny to the input of the forklift motor.
We'll need to make a custom yoke that will go on the driveshaft of the motor. This will most-likely mean using the splines from the forklift drum brake to weld to a shortened yoke. Then, the yoke will match the motor on one end, and the drive-shaft u-joint on the other. The driveshaft will be shortened, re-using the components on both ends, but chopping the length of the motor out of the middle. The motor and new short driveshaft will be the exact length of the stock drive shaft.
To mount the motor, I'll add two cross-pieces to the frame of the truck to hold it in place. Ideally, I want to make it so that both the transmission and the motor each have their own supports to the frame of the truck.
That way, I will be able to swap between the motor/short-shaft and the stock shaft anytime I want.
That even means I might be able to drive the truck with JUST the motor without an engine and transmission even in it yet! (I know this sound rediculous, but there are times when it would just be SO nice to be able to move in and out of my garage under its own power!)
I'm also thinking that with the modifications I would have to do to the gas tank to convert to diesel, the better way to go is with a SMALL fuel tank in the bed of the truck. That frees up space under the bed for batteries, and a fuel cell would have it's own large gas cap (which would fit a diesel hose) and I could then reuse the original gas filler port as a cover for the charger power inlet!
I'm starting to feel pretty good about this project - that I'm not totally crazy and that this IS something that I can do.
I'll still need LOTS more help. If anyone wants to start building a 1000 amp motor controller or high-voltage charger for this project, please do!
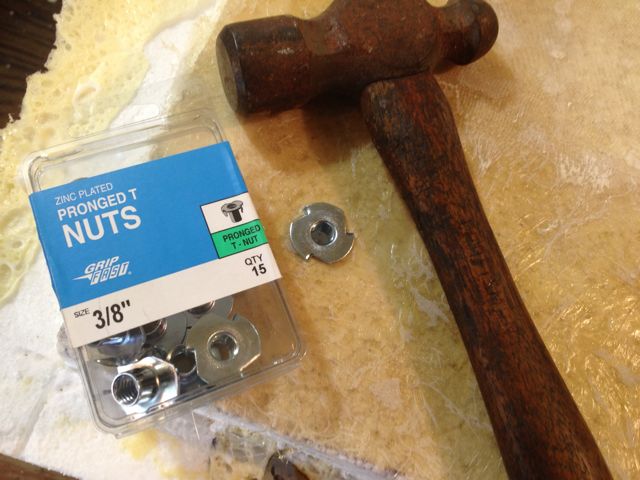
T-Nuts as "multipurpose holes" for the underside of the cover.
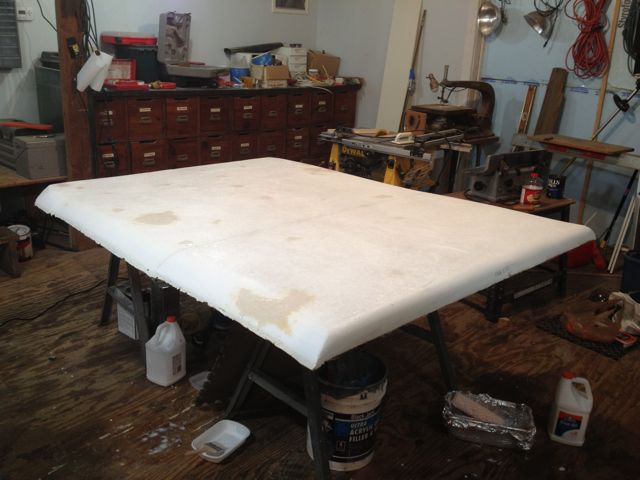
The foam cover, with holes filled in with wood filler, including a large gash I performed with the belt-sander.

A visual discussion of the driveline concept.
More adventures of the day at my blog.
http://300mpg.org/2012/12/08/supertr...s-getting-fun/
-Ben