This project has felt like pretty smooth sailing so far, but yesterday I got snagged on the compound curvature for the two front skin corners.
Transfer X,Y coordinates from the drawing using a pair of tape measures.
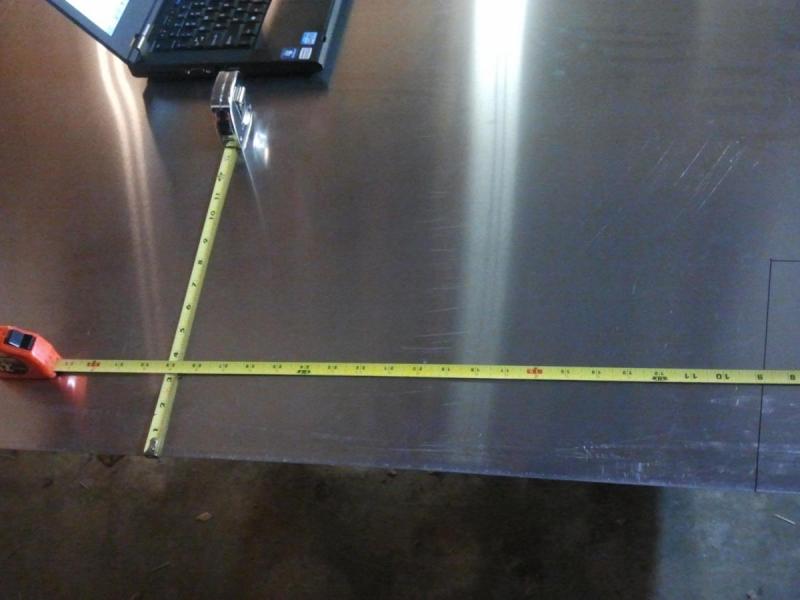
By the way, the PDF drawings I posted on my server have a projected view for this part, which is wrong. Thankfully, I caught the mistake and changed it to an 'unfolded' view before I started snipping, otherwise it would be 4" short on two edges.
Then trace it out to make a copy for the second half.
Here's the trouble:
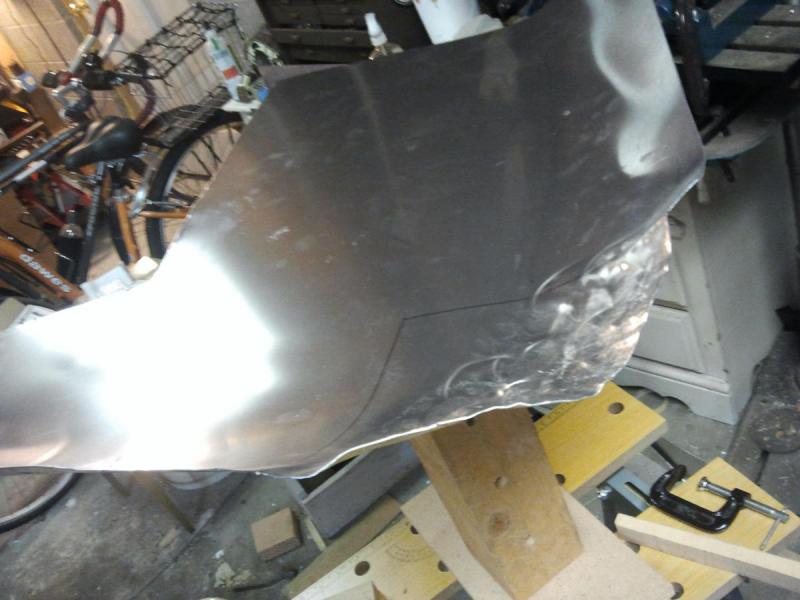
'Stump' shrinking - the method I used to make the little practice bowl shown earlier - didn't work. ... Or maybe it worked a little since I see a little compound curvature in this corner, but it's never going to make it to the required acute angle. I think the problem is primarily the switch to a heavier gauge sheet, 0.032" instead of 0.019".
I'm also not happy with the amount of stretching inherent to the stump method. So instead of trying to adapt to the heavier gauge, I tried making a DIY tuck shrinking jig with some steel rod and angle bracket, but also failed there on the first two attempts.
Time to reevaluate - this piece is in bad shape now - do I have enough scrap sheet to start over? Yes. So this bungled piece can be called practice. I still feel like I'll be happier with aluminum corners vs fiberglass, so I'm going to make another attempt at tuck shrinking next week. If I just can't get it to go, the backup plan is to snip out the corners and do the compound curvature with foam/fiberglass.