Maybe if you heated the plastic uniformly in a very hot bath of water then put it over a relatively smooth form til it cools. It would seem that would make it less prone to sharp creases. But the very nature of corrugated material would still have it creasing. Though after heat forming, (sort of) it may crease less severely in several places over a larger area rather than large creases in only a few places. What you would have then is a surface with several small flat surfaces something like the planking on a boat giving it a smoother curvature rather than only a few flat surfaces like a barn roof.
I've done CF & FG in wet lay up in a form that I made for the curved top piece and CF & FG wet lay up on the glass of an old storm door of all things. And it gives flat panels that are glass smooth. The curved form gives pieces with an almost mirror smooth finish as well. They are simply pop riveted to hardware store aluminum angles and seams are covered with reflective tape.
The Carbon Fiber and Fiberglass cloth materials I got for dirt cheap some years ago off ebay. So it's not like it has that super high quality high dollar CF look. I am thinking of roughing that glossy finish with some very fine sandpaper so that a light color paint will stick better. That shiny black carbon fiber sure looks nice but it gets HOT HOT HOT!! in the sunlight
My curved form developed a crack about a foot from the narrow end during the winter. I stop drilled it to prevent the crack from migrating further. My bad as I did not secure it fully before putting in away. Still it is quite usable; It's just that If pieces are to be made so that it comes all the way to a point at the end, then that last foot of the shape would need to be made using a few parts. No big deal really IMO. I plan to use it to make a Kammback style fairing for one of my other scooters.
Here is a link to the thread about the 2007 Honda Reflex I have been working on. It is only a little further on in progress since these pics were taken but I don't have current pics yet.
http://ecomodder.com/forum/showthrea...tml#post378656
What kind of dimensions are you needing for the curved top piece? Wide end height? X width? Angle that it has from top down to the bottom --- Narrow end height X width and angle down from top to bottom (if important) ---
I don't have the exact measurements on hand of the curved top section that I have done here but the front is about 24" wide X 16 or 17" tall and whatever shallow angle deviation from 90* that you can see in the pic. The narrow end was only a few inches tall and about 1.5 inches wide. Bottom base line is about 68" and at the top of the curve it is about 72" long. Of course any pieces I do now would be about a foot less in length along the base and the narrow end at that point would be about 5.5 inches wide.
Just an added note; the material I've used has some flexibility and the width and height at the front wide end can be changed some merely by squeezing it together. It is not overly heavy or floppy and will stay up on its own yet becomes surprisingly rigid with the addition of a bulkhead and the aluminum angle stringers and a couple cross pieces.
Here is a pic of the first 2 pieces of composite work I have ever done. the first got wrinkles because I brought the form out into the sunlight to warm it to help with the cure process. (so I thought) Then at night the temps went down and the form shrank a little causing the lay up to be compressed and subsequently wrinkled. The 2nd far better engineered piece came out that way because I kept the temperature a steady 85* for the entire lay up cure time. Big difference in outcome. It's a learning process.
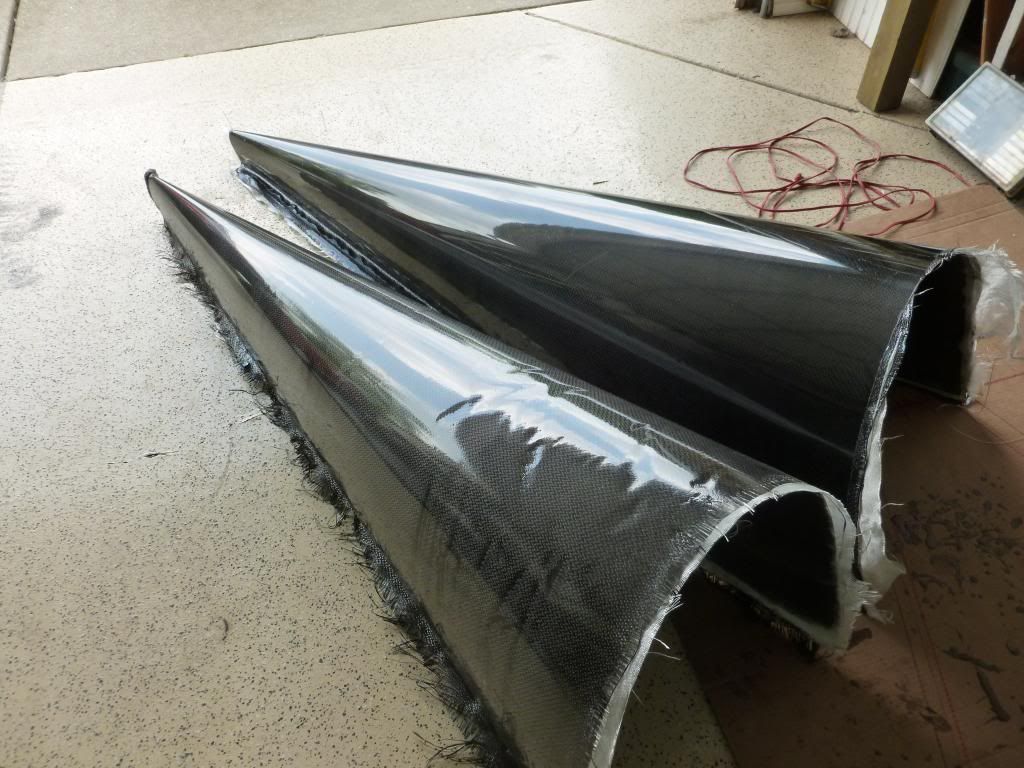