I would like this to be an open source project. By that I mean, that if anybody would like to contribute, or take what I have and run with it -- as long as you keep me up to date, then great.
Here's a photo of the revised 1/24th scale (1/2" = 1') wooden model and the drawings that I've been working on:
Here's a start on the 3D model -- I have drawn what could be aluminum ribs that would be part of a monocoque chassis (very similar to the way acrobatic airplanes are made):
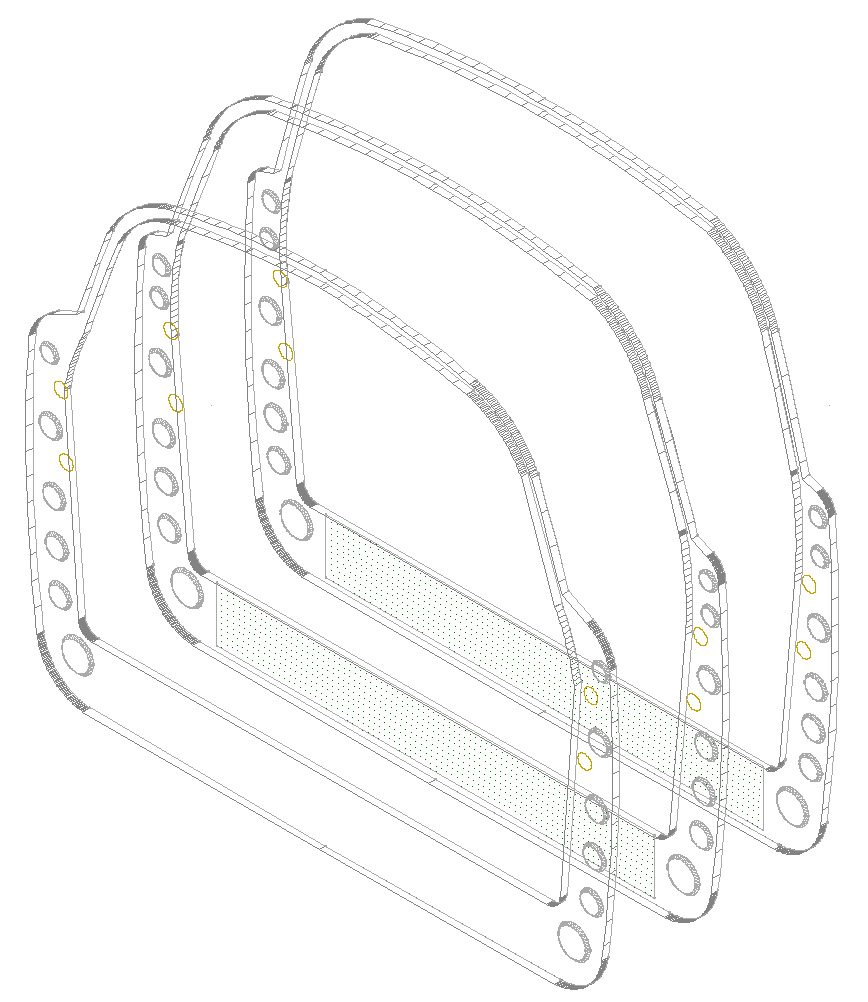
The rib on the right is at the highest point on the roof, and they are 1' apart (for modeling purposes, anyway). The large rectangular hole in the floor of the two is for the battery pack. The battery pack is the 4' square by 6" deep shaded rectangle on the drawings.
At this point, I'm thinking it would be better and faster to have my wooden model 3D scanned and have a mesh/surface model made. Does anyboy have any experience with this? Here's an outfit that can do it for ~$100-200:
3D Scan Services LLC - Affordable 3D Scanning and Reverse Engineering Services, but I'm hoping to find a place that is much closer to Massachusetts, where I live.
CarBEN Concept EV
An Open Source Project
Project Outline
Design and build an uber-efficient electric car; that has very low aerodynamic drag, as low weight as possible, is designed with good safety and crash protection, is practical to drive (i.e. it is not too big and has nimble handling), and I would like it to carry 4-5 people. By the way, the reason I chose the name CarBEN: it is a play on the word carbon (I want to not waste any), and the change in spelling are my initials backwards... :-)
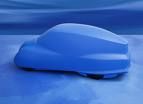
The basis for the aerodynamics is an early clay model of the Mercedes Bionic car (aka “Boxfish”) that was itself based on the boxfish. The tested coefficient of drag (Cd) of this model was an amazing 0.095 (
Automotive Engineer PLUS - Mercedes-Benz) and it seems like a great place to start! The later Bionic car had a Cd of 0.19, which is still very good; but the open wheels and wider shape in the back are the primary reasons for the increase in drag. Another design that inspired a lot of the CarBEN design is the Schlörwagen – a very aerodynamic design from 1939.
My idea that will allow the wheels to remain covered, and therefore (hopefully) achieve a Cd nearer to the blue model than to the Bionic car, is to have articulated front wheel covers that move with the wheels in sharper turns. I'll get more into the details of how this could work later on.
To achieve low weight, I think the ideal structure would be carbon fiber reinforced plastic. But this is difficult for me to work with, as I have no experience with it, and I think the prospect of making molds and the fumes, etc. is daunting. I've also considered welding a steel tube chassis, and then make either a fiberglass or aluminum body. But I think this would be heavier, and while I have access to a MIG welder; it is not as good as an aluminum monocoque chassis.
I got the idea for how to do this from seeing a friend who is building an airplane from scratch. It is a 2 seat acrobatic capable, and the dry weight (including the 4 cylinder 80HP engine) is between 570 and 620 pounds. I think the process he is using, which plotting out full size templates, and then forming the 6061-T6 sheets into the ribs and the skin; using wooden forms – makes a lot of sense to use this method to build this car.
Aluminum is fully recyclable, it is not dusty, has no fumes, and only requires a small bandsaw, a pair of “pleating” pliers, a soft hammer, and riveting tools. If I start with a 3D CAD model and drawings generated from that, the templates will be accurate. The resulting chassis should be lighter than I could manage with steel, and it forms the body at the same time.
Starting with the Sonex airplane (
Sonex -- The Sport Aircraft Reality Check!) and its weight of 620 pounds (~130 pounds for the engine is included in that) – the 22' wingspan and 18' long fuselage have roughly similar surface area to my CarBEN design and so it should weigh about the same (490 pounds). The AC electric motor and mechanical drive train are maybe a little heavier than the plane's engine; say 150 pounds. Add the four wheels, brakes, and the suspension (say 250 pounds) and the battery pack (say 400 – 600 pounds), the seats (which will be quite light – more later) and miscellaneous stuff will add 150 pounds. The the total vehicle weight could be in the 1450-1650 pound range. I would be very happy with anything under 1800 pounds.
The first order of business is to get the overall chassis to be as low drag as possible: I can loft a 3D CAD model from the wooden model I have made, but I think it would be better/faster/cheaper to have the model 3D scanned and use the mesh model for virtual aerodynamic testing. A program that can do 3D flow would be very important to check the form and to adjust it to lower the drag as much as possible without making it impractical to drive. i.e. I'm 6'-4” and I want to fit comfortably, and I need to fit my family.
For the safety considerations, the first thing I am doing is making the structure surround the passengers, and in order not to weaken it with doors, like most cars do. Like all design decisions, this involves some compromise, and I have been considering what some other designers have done: both the VW 1L and the FVT eVaro have canopies (like a jet fighter airplane), so that the structure around the passengers is continuous; the compromise comes in inclement weather, as the roof is not over the seats. Another car design that uses an unusual door and entry method is the Loremo; the entire windshield and hood hinge up (from the front) and you step over the side and pull the door back down in place. This also involves the steering wheel and column hinging up and out of the way with the door. The passengers get in through the rear hatch (and they sit facing backwards).
So, the initial door concept I am hoping to use is: in order to maintain a wraparound structure for safety, there is a single door in the rear of the CarBEN. It has two parts: a sloped hatch that is approximately the back 1/3 of the roof; it lifts up but remains (mostly) covering the opening from precipitation. The rear fascia of the car is a pair of small hinged doors that swing out. This is a a good a place as any to put in the drawing:
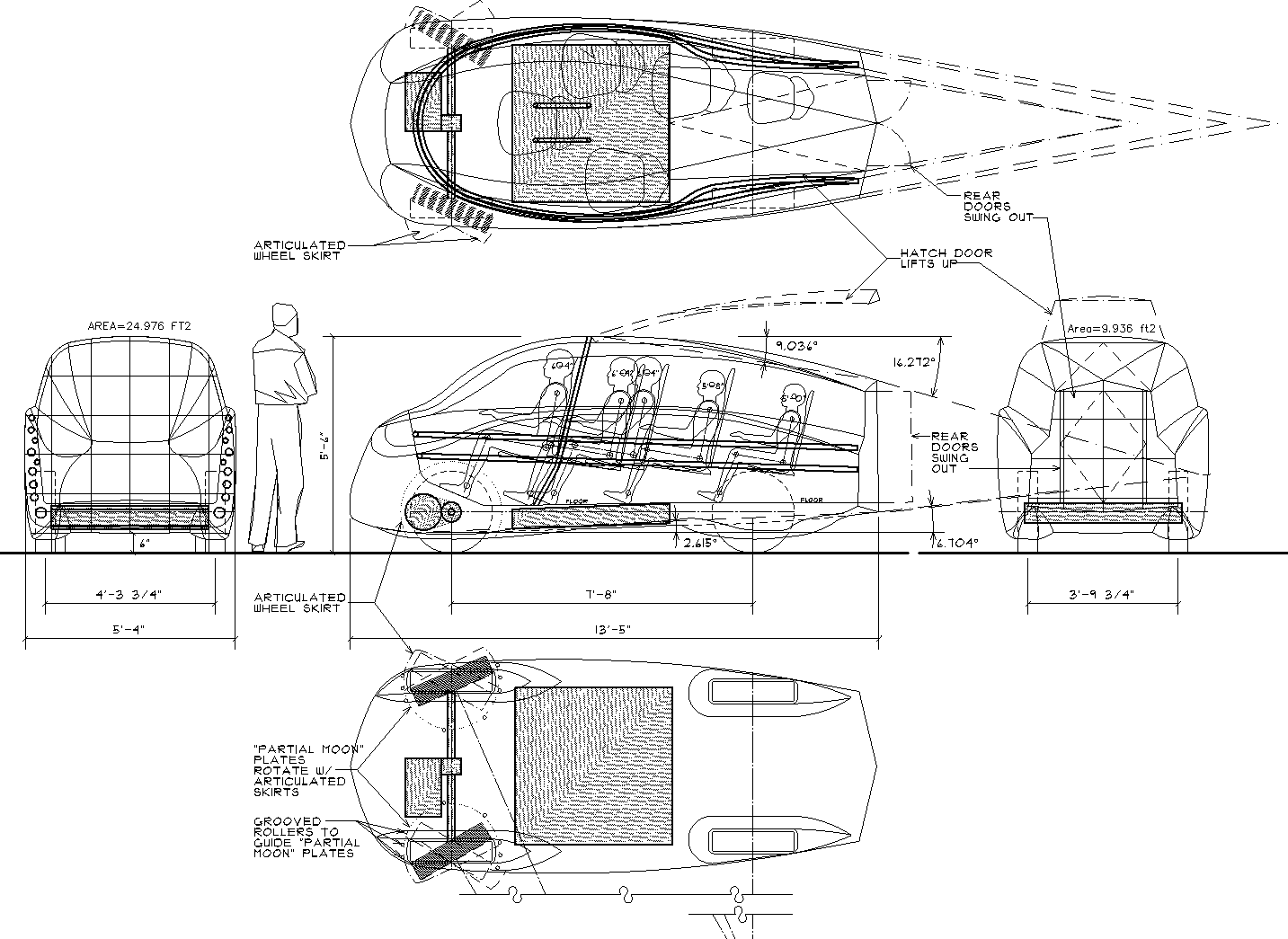
To get in the CarBEN, people would step up to the floor, and then turn to close the back doors, and the walk up the “aisle” to their seat. (This hopefully explains the staggered seat placement?) The overhead hatch would be closed – the details need to be worked out. If this door idea is not workable, or involves too much effort, then the fallback solution is to have conventional side doors – but I would use 3 or more latches (instead of the usual one) so that the door has 5 (or more) points of attachment (instead of the usual 3) so that the opening is not unduly weakened, and the passengers would be well protected from side impacts.
The other key solution to getting the CarBEN to work within a very low drag chassis, is the idea of articulated front wheel skirts (see the top, side and bottom views in the drawing). These consist of a ¾ moon panel on the bottom (shown with a dotted line) and another ¾ moon panel on the outside of the front wheel (also shown with a dotted line). There is a slot in the bottom panel where the wheel protrudes out, and there is an inner fender and curved panels that keep the wheel covered even when the steering is all the way to one lock or the other. The suspension motion of the wheel does not move the skirt assembly – the tire moves up and down through the slot and within the inner fender. The whole assembly pivots on grooved rollers around the edge of the bottom panel (see the small circles on the bottom view drawing) and a pivot at the top of the inner fender.
The steering pushrods are connected to the skirt assembly, and swing it with the wheel when the steering angle is sharper than needed for highway driving. So, at high speeds the aerodynamic shape remains unchanged, but at low(er) speeds when sharper steering angles are needed, the panels move to maintain clearance around the wheels. This is the biggest compromise made in the Schlörwagen design – they made the front wide enough to enclose the wheels even when they are at either steering lock. The Schlörwagen is 2.1 meters wide (6'-11”) which has a large affect on the area and hence the drag (CdA) and the car is wide; making it more difficult to drive. It also means there would be more body roll than would otherwise happen.
The battery pack (the 4' x 4' x 6”rectangle) should fit in the floor, between the four wheels. The AC electric drive train is a typical front wheel drive system; which will provide the best ability to have regenerative braking, to regain some of the power. I intend to use a super capacitor in parallel with the battery pack, which allows higher current to be absorbed from regenerative braking to be absorbed, and it can provide bursts of high current for acceleration, greatly reducing the battery load during charging and discharging, while driving. The folks at
ChargeCar (at Carnegie Mellon) are working on enhancing this kind of system with “smart” programing that uses data from your commonly driven routes (using GPS to locate where you are driving) and elevation data to “anticipate” how to best manage the regenerated power, and to make the best use of the supercapacitor; as a power cache.
(to be continued)