06-06-2015, 03:38 AM
|
#11 (permalink)
|
Banned
Join Date: Oct 2009
Location: Fort Worth, Texas
Posts: 2,442
Thanks: 1,422
Thanked 737 Times in 557 Posts
|
To Phils list I would add that lower, not just upper, horizontal surfaces should be radiused.
Fully independent suspension where the wheel face is at least parallel to sidewall if not further out (trailer stability, which is resistance to winds and to tripping hazards)
FWIW, I'd stick with Dodge turbo diesel trucks as mpg is always potentially higher as it has been since 1989.
A 5er or gooseneck hitch to distribute weight efficiently on the truck and to clise the truck/trailer gap. I've tried to cover more in other posts on either threads.
Really, though, the problem here is emotional, not technical. The change to the annual fuel budget is not that great, is it?
One must know ones annual fuel cost. The way to pay the 40% FE penalty while towing is to get daily driver costs down. I improved my city mpg by 20% in driving both fewer miles to accomplish the same tasks, and by driving those remaining miles at a higher skill level. Cut miles driven first (cold starts), and strive for highest mpg second. Combine trips and run a planned route to accomplish them. UPS and FedEx drivers do this. No left turns, for example. My savings were such that on an annual basis this would completely underwrite the fuel cost of up to 5,000-miles of towing my 35' travel trailer under ideal conditions.
The best combined rig is the one with the lowest long term costs. A used high quality trailer would be my choice. Same for a Dodge with manual transmission, preferably pre-emission. The 666 Rule: 60-mph, with 6-psi boost or less and 600F EGT. Towing will be harder, but any work toward smoothing transition from truck to trailer will pay. Same for trailer tail.
Towing is generally a 30-40% penalty at a reasonable towing speed. Which is always under 65-mph due to lousy vehicle dynamics and cheap (drum) trailer brakes. Comparisons between solo and towing should be made over a 2-300 mile course at the same speed and with the use of cruise control.
Know your actual costs, attack the weak points, and make solid numbers for predictions. Be painstaking about mechanical details on both vehicles. Those minor while solo are hugely magnified in towing.
As above, see my other posts.
Last edited by slowmover; 06-06-2015 at 03:50 AM..
|
|
|
The Following 3 Users Say Thank You to slowmover For This Useful Post:
|
|
Today
|
|
|
Other popular topics in this forum...
|
|
|
06-06-2015, 01:02 PM
|
#12 (permalink)
|
Master EcoModder
Join Date: Jan 2008
Location: Sanger,Texas,U.S.A.
Posts: 16,534
Thanks: 24,520
Thanked 7,438 Times in 4,818 Posts
|
would it
Quote:
Originally Posted by jray3
That Don-Bur trailer raises an old question for the pending rebuild of my old and very square trailer. If I increase the frontal area by 'adding a bubble' matching the template atop the original square-edged roof, or for that matter, the sides, would it be reasonable to expect a net improvement? I think so, and cutting down the stout frame of my box-body trailer would be much harder than adding to it (and gaining some storage cavities).
|
Hucho says not to do it,then Don Bur does it and claims an overall drag reduction.
If we take Don Bur's claim at face value,then it suggests that the benefit of the body camber far out shadows the penalty of the added frontal area.
Until another player publishes results of like technology we don't have a lot to decide by. 
__________________
Photobucket album: http://s1271.photobucket.com/albums/jj622/aerohead2/
|
|
|
The Following 2 Users Say Thank You to aerohead For This Useful Post:
|
|
06-06-2015, 01:20 PM
|
#13 (permalink)
|
Master EcoModder
Join Date: Jan 2008
Location: Sanger,Texas,U.S.A.
Posts: 16,534
Thanks: 24,520
Thanked 7,438 Times in 4,818 Posts
|
evolution
Quote:
Originally Posted by RACERSNUT
It seems that I've got some reading to do. Thank you all for the links and references.
I know that most of the big rig trailer information would apply to a plain jane cargo trailer. Although, by the looks of things.......it seems that the general enclosed trailer industry as a whole falls far short of what could be a huge improvement in aerodynamics. Not that I'm opposed to working for something to improve mileage,....but at some point one would think there would be an evolution of sorts. Well at least something more than a V-nose design.
I'm familiar with the template that's offered as a tool. It would certainly be interesting if the Cargo Trailer industry would even consider such a thing.
Again, thanks for the information!
|
In 'FAIRING WELL',Gelzer discusses the cultural bias against 'thinkers,' advanced technology,and how consumers are attached to 'man it up.' Just add more horsepower.
Fleet operators couldn't give a ---t what an 18-wheeler looks like,they're business men,just looking at the bottom line.
Some drivers, on the other hand,express open hostility towards anything that isn't conventional.
35-years later,we still don't have a decent trailer for sale in the U.S.,but it's not because people haven't tried.
Adam,the trucker,can't stand the sight of Eve.
This would be a scientific response to a low-drag trailer challenge
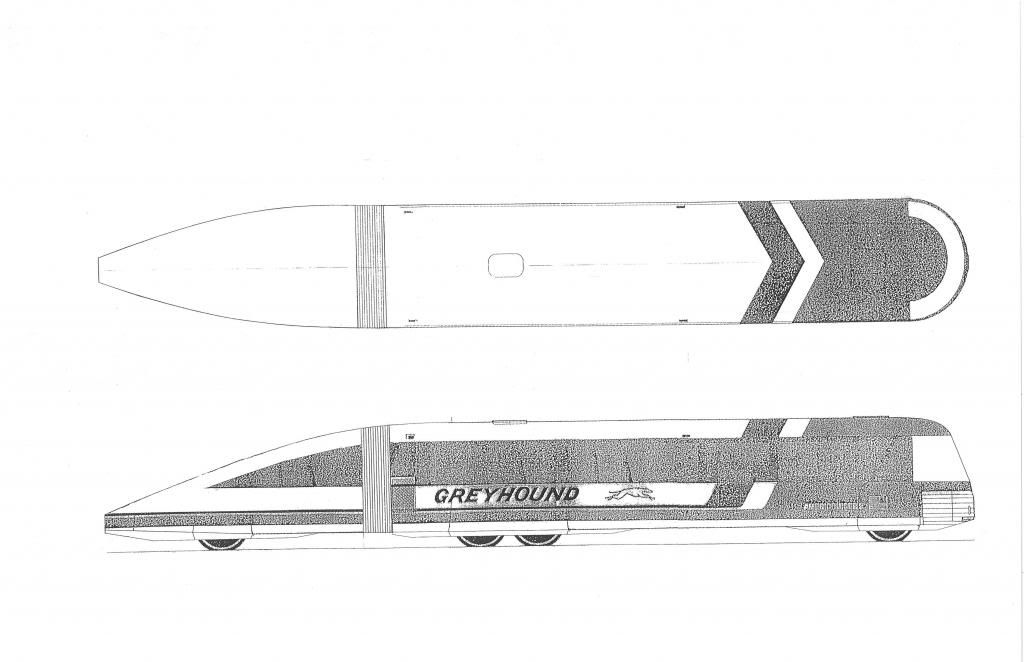
It's okay for Great White sharks,land speed record cars,and American Bald Eagles,but never good enough for American truckers.Those Eagles are sissies!
__________________
Photobucket album: http://s1271.photobucket.com/albums/jj622/aerohead2/
Last edited by aerohead; 06-06-2015 at 01:26 PM..
Reason: add more angst
|
|
|
The Following 2 Users Say Thank You to aerohead For This Useful Post:
|
|
06-07-2015, 12:00 PM
|
#14 (permalink)
|
aero enthusiast
Join Date: Jan 2015
Location: Saskatchewan, Canada
Posts: 92
Thanks: 157
Thanked 67 Times in 41 Posts
|
The Don bur designed trailer was included in this interesting thesis on aerodynamic devices for semi trailers:
http:// publications.lib.chalmers.se...ext/133659.pdf
EDIT tried to update link, but if no luck search :cfd chalmers 133659.pdf
Last edited by rumdog; 06-08-2015 at 09:51 AM..
|
|
|
The Following User Says Thank You to rumdog For This Useful Post:
|
|
06-07-2015, 12:15 PM
|
#15 (permalink)
|
EcoModding Lurker
Join Date: Jan 2013
Location: USA
Posts: 6
Thanks: 6
Thanked 1 Time in 1 Post
|
freebeard,.........thank you for the PolyMetal idea. I'd never heard of it before. How hard is it to work with? Bend in a sheet metal brake? The box van idea is something I've kicked around. Maybe an old Penske van? And that drawing "1947 Roswell" is pretty cool.
Slowmover,........a Dodge diesel truck is certainly an option. Although, I'm curious as to why a non-emissions truck would be preferable? (My everyday job is doing emissions testing on stationary engines for the natural gas industry.) A truck has not been purchased yet,......so it is on the consideration list. I used a F-250 as an example of what I'd had in mind earlier.
Aerohead, ....I couldn't have said it better. I'm going to purchase that book this week.......more reading to do I suppose. The more I learn, the more I find out how much I didn't know.............
In the end, it's clear that I've come to the right place to put my mind right. Thank you all.
|
|
|
06-07-2015, 03:27 PM
|
#16 (permalink)
|
Master EcoModder
Join Date: Aug 2012
Location: northwest of normal
Posts: 29,422
Thanks: 8,369
Thanked 9,128 Times in 7,537 Posts
|
www.nudo.com/p_polymetal.php
https://www.grimco.com/Products.aspx?cid=0198
http://www.alumapanel.com/subcategories.cfm?lines_ID=3
I worked with scraps of PolyMetal and a hand shear/brake/roller. Larger pieces would require different tools, like an edge roller. I was able to shear and roll foot-wide pieces by hand at an 18" lever arm. Braking the angle ruptured the outer aluminum skin, which didn't affect my demonstration. Scoring or a shallow cut would relieve that. I'm not sure what tool would score it—short of a broad chisel and hammer, but remove one skin and about half the thickness of the plastic would be about right. Then you could glue or solder the inner edge.
I like the Roswell. There's a way to make yurt-like pods of thin plywood like that. I adapted the idea to The Template that is so popular around these parts.
This actually follows The Template at very low resolution. The front angle is 45° and the rear (if the truncation were extended) is 45°. Close enough to the theoretical ideal of 44 1/2°, which number came from a wind tunnel and I'm convinced is a measurement error.
Anyway, scaled up for your purposes, it might have a longer center section (with internal wheelwells) and a shorter truncation to fit a bigger back door. As you shrink the trailer around the car, it will get harder to get it in and out. If the width 3' above the floor is the widest part that might help. If I was doing this, I'd want a 2-piece floor with the front section having arms that reach back to a pivot line in the middle of the back section. Then you could open the door[s] and drop the back of the floor to the ground. I guess it would be like a roll-back truck. With an automated winch so you don't have to drive the car in and then open the door to get out.
Last edited by freebeard; 06-07-2015 at 03:38 PM..
|
|
|
The Following User Says Thank You to freebeard For This Useful Post:
|
|
06-07-2015, 08:03 PM
|
#17 (permalink)
|
EcoModding Lurker
Join Date: Jan 2013
Location: USA
Posts: 6
Thanks: 6
Thanked 1 Time in 1 Post
|
Rumdog, .....I can't see the link. Sorry.
Freebeard, .....in another career I spent some time as a Plastics Process/Design engineer. With the plastic core made of polyethylene, a strip heater could be used to heat the local area where a bend is to be made. The "Glass Transition Temperature" , the point where the polyethylene is between a solid and semi-viscous processing temperature should be in the neighborhood of 275-310 Deg. F. I'm thinking that this ought to be below the point where the alum. skin would crystalize and work harden. Thoughts? I'm really liking the pictures of your model. It looks something like the Decoliner that the Blastolene brothers did just a few years back.
http://silodrome.com/decoliner-blastolene/
|
|
|
06-07-2015, 08:49 PM
|
#18 (permalink)
|
Master EcoModder
Join Date: Aug 2012
Location: northwest of normal
Posts: 29,422
Thanks: 8,369
Thanked 9,128 Times in 7,537 Posts
|
Mentioning me in the same breath as Randy Grubb is flattering. Google isn't giving up much on work-hardening aluminum, but this abstract suggests the curves for work hardening and creep cross at 1/2 melting temperature (1,221°F (660.3°C)).
Did I mention that one of the advantages of PolyMetal is that it come in 4x8, 5x8 and 5x10 sheets? That means you could make a 5' section with one seam down the center top.
slowmover -- What think you of this:
http://justacarguy.blogspot.com/2015/06/going-in-style-with-camper-and-both.html
|
|
|
|