09-10-2014, 08:29 PM
|
#31 (permalink)
|
EcoModder In Training
Join Date: Jul 2014
Location: Cleveland, Ohio
Posts: 20
Thanks: 13
Thanked 3 Times in 2 Posts
|
Quote:
Originally Posted by freebeard
I like the cardboard egg-crating. But when people say PVC, I shudder. Why not get green timber bamboo, make your finalized shape and bake it?
|
How well will bamboo hold up in both hot and cold weather, rain, humidity, etc.?
Quote:
Originally Posted by freebeard
The one in the middle is called a 'squircle'.
|
That sounds like a technical term; I like it.
Quote:
Originally Posted by freebeard
I can get a complete boattail in 3 additional feet on a 12' car.
|
Haha, in 3 feet, I can only get about to about 30% of a full tail based on the template, since my tail end is fairly squared off. Your frame certainly looks nice. Maybe I could make arcs with thin aluminum barstock instead of bamboo for better weather resistance.
__________________
"On the 8th day, God created kammbacks. And God saw that it was good."
-Genesis 1:32
|
|
|
Today
|
|
|
Other popular topics in this forum...
|
|
|
09-10-2014, 09:58 PM
|
#32 (permalink)
|
Master EcoModder
Join Date: Aug 2012
Location: northwest of normal
Posts: 28,978
Thanks: 8,225
Thanked 8,995 Times in 7,431 Posts
|
Quote:
How well will bamboo hold up in both hot and cold weather, rain, humidity, etc.?
|
As well as the PVC in sunlight.
Green Building - Sustainable Products & Construction Materials | Cali Bamboo
Quote:
Thanks to its unique composition, bamboo is naturally designed for strength...
As a result, in structural engineering tests bamboo has been shown to have...
Higher tensile strength than many alloys of steel
Higher compressive strength than many mixtures of concrete
Higher strength-to-weight ratio than graphite
|
But that's just my reaction to evil, evil PVC. Were it I, I'd get aluminum flashing metal and roll strips into 120° of a circle, cut the side pieces and roll the edges on a longer radius and rivet it all together. That would closely approximate the squircle.
Quote:
That sounds like a technical term; I like it.
|
Technically, it's a special case of the superellipse.
The Squircle Is The Hottest Thing In Car Design Right Now - Jalopnik
Quote:
Haha, in 3 feet, I can only get about to about 30% of a full tail based on the template, since my tail end is fairly squared off.
|
I felt bad when I wrote that. It was almost like a boast.
|
|
|
The Following User Says Thank You to freebeard For This Useful Post:
|
|
09-10-2014, 10:18 PM
|
#33 (permalink)
|
EcoModder In Training
Join Date: Jul 2014
Location: Cleveland, Ohio
Posts: 20
Thanks: 13
Thanked 3 Times in 2 Posts
|
Quote:
Originally Posted by freebeard
As well as the PVC in sunlight. 
|
Touché. Thanks.
__________________
"On the 8th day, God created kammbacks. And God saw that it was good."
-Genesis 1:32
|
|
|
09-11-2014, 05:12 PM
|
#34 (permalink)
|
Lots of Questions
Join Date: Jan 2013
Location: San Jose
Posts: 665
Thanks: 343
Thanked 101 Times in 79 Posts
|
Quote:
Originally Posted by UnicycleDan
I hesitate to ask this since they're so expensive, but would a ScanGauge make my testing easier/better? Could I use it and go at a constant speed (maybe 60mph, for example) to get the angle that gives the best FE? Would that work?
|
I think the SG is a good idea for determininh best practices, however, if you only use that to determine the best angle for the kamm, you will be blindly shooting in the dark trying to find the best angle. I think the tuft testing is the best way so that you can determine what's best for every square inch of the kamm.
You can get an UltraGauge or even a bluetooth adapter and a Torque-like app instead of the SG at a much much lower cost.
__________________
Don't forget to like our Facebook page!
Best EM Quotes:
Quote:
Originally Posted by aerohead
It has been said, that if you peel the duct tape back on Earth's equator, you'll find that the two hemispheres are held together with J B Weld.
|
Quote:
Originally Posted by Dan9
subscribed with a soda.
|
Quote:
Originally Posted by aerohead
If you're burning,and someone throws gasoline on you,there will be a localized cooling effect, but you're still on fire.
|
|
|
|
The Following User Says Thank You to jeff88 For This Useful Post:
|
|
09-28-2014, 10:09 PM
|
#35 (permalink)
|
EcoModder In Training
Join Date: Jul 2014
Location: Cleveland, Ohio
Posts: 20
Thanks: 13
Thanked 3 Times in 2 Posts
|
I did some more testing over the past couple weeks. Tuft testing showed I was able to get not fully, but mostly, laminar flow on the top Kammback panel at a 9-degree decline at 65mph. I chose 65 because I only feel comfortable/safe driving 5 below the speed limit on the highway when people around you are going 5-10 over.
For the side panels, I had attached, but somewhat turbulent flow, even at a low inward angle of only a couple degrees. I added a few tufts to the car and found out that the airflow is already a little bit turbulent along the side of my car, too. The kammback at least was not making flow worse, since the turbulence was about the same...
Using my scangage, I saw no appreciable MPG difference between when I had the cardboard kammback on vs. just the stock car. I ran the same 4-mile stretch of highway repeatedly, holding constant speeds and restarting the gage tripmeter at the same points every time, for consistency.
Questions:
1) With attached but somewhat turbulent flow along the side panels, are they still providing me an aerodynamic benefit with a 2-3 degree inward angle, or is my top panel the only portion worth building?
2) Is the tuft-testing goal to maintain laminar flow or just attached flow? Can I keep increasing my panel angles until I have detached flow, then back up a little, or is there no point to increase the 2-3 degree side panel angle since I already have turbulent flow?
3) If I didn't see any change between my scangage average trip MPGs over the consistent 4-mile stretch with and without the cardboard prototype, is it even worth building at all? Or is this somehow normal to not see a scangage improvement, but to see an actual tank improvement?
I've done different types of testing with this cardboard kammback 4 times, now, and I'm unfortunately starting to get a little frustrated with it - a lot of work, time, extra miles, but no visible FE improvement. Maybe it's because I can only get down to the 30% mark on the aero template, but I assumed that would at least make some difference since I'm extending my car by 3 feet. Input and suggestions would be appreciated, thanks.
__________________
"On the 8th day, God created kammbacks. And God saw that it was good."
-Genesis 1:32
Last edited by UnicycleDan; 09-28-2014 at 11:07 PM..
|
|
|
09-29-2014, 02:33 AM
|
#36 (permalink)
|
Master EcoModder
Join Date: Aug 2012
Location: northwest of normal
Posts: 28,978
Thanks: 8,225
Thanked 8,995 Times in 7,431 Posts
|
If the mileage isn't panning out, how does it feel? Any difference when you meet/pass a big truck (cattle trucks are the worst, ask aerohead)?
IMHO means In My Humble Opinion: What you have is a wake filler that is only half there. Thinking about a specific angle obfuscates the fact that the ideal, The Template, is a compound curved form. Any angles are merely tangential. Laminar flow ends at about the hood ornament. From there back it's turbulent flow, especially on the downwind side. So you are working with attached turbulent flow.
If the cardboard was cut with curved edges it would flex into simple curves. A curve that starts around the back of the quarter-window and front of the taillight*, as a smooth tangent to the body and curves down and in to the section you terminate at now, should be more effective. The turbulence down the sides (possibly from the front wheel well) would needs some length to reattach. Instead it gets tripped again.
Your vehicle already has a Kamm-back, you're wanting to return it to a partial boattail.
It's a tough problem. I know a solution, but it would be painful:
One of my favorite cars, the Volkswagen Golf GTI w12 650. The Golf is a Kamm-back, like yours, but this has been converted to a bubble-top coupe wit only the skeleton of the original top left. That's what it takes. It has a 200mph top speed.
The wheelwells and underbody (diverter and difusser) offer as much opportunity as your 30% tail.
* I know, I know.
|
|
|
The Following User Says Thank You to freebeard For This Useful Post:
|
|
09-29-2014, 07:17 PM
|
#37 (permalink)
|
Master EcoModder
Join Date: Jan 2008
Location: Sanger,Texas,U.S.A.
Posts: 16,401
Thanks: 24,469
Thanked 7,410 Times in 4,800 Posts
|
Kammback
Here is Kamm's last 'Kammback' from the late 1960s.
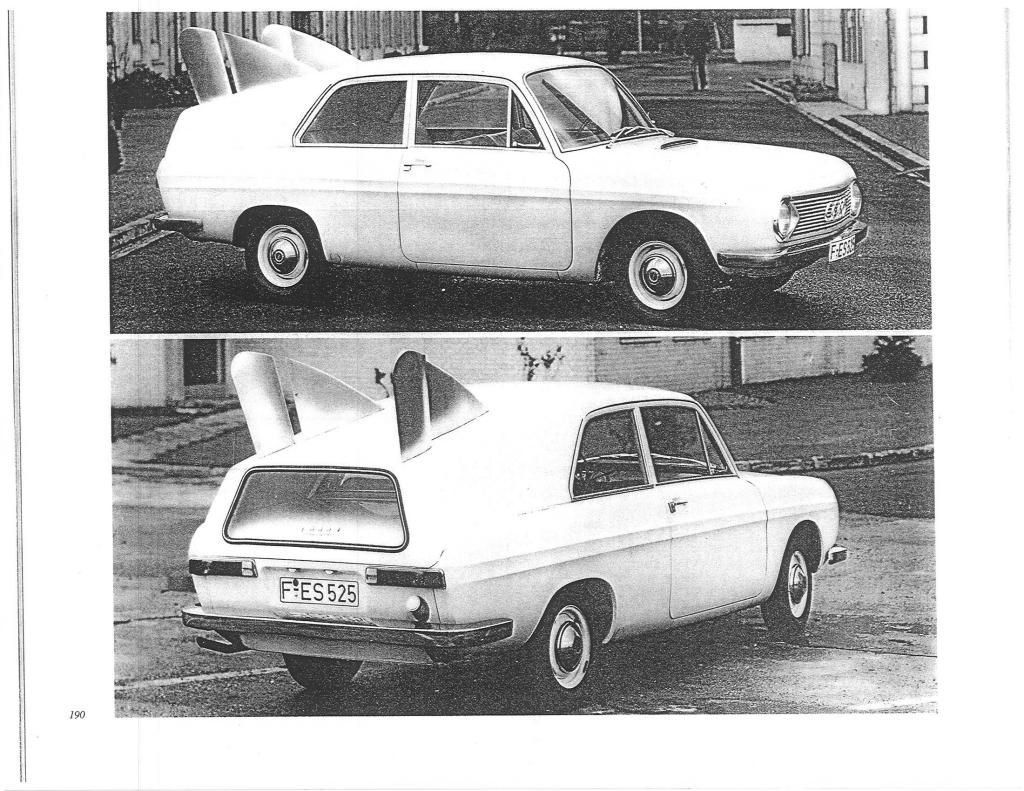
You can see that it is perfectly integrated into the body with seamless transition.The air needs this 'perfection' in order to protect the boundary layer,which determined whether or not you'll have separation.
Your cardboard mockup is more like a box-cavity,and for it to work,it needs to be as low as the bottom of your bumpers bottom,and it needs a 'floor'.It cannot be open on the bottom unless there is a back on it,and the back is airtight.
The trailing edges of your box would be at the same place as it it were a perfect boat tail Kamm extension.
The top edge would be like on the XL1 or 'Template'
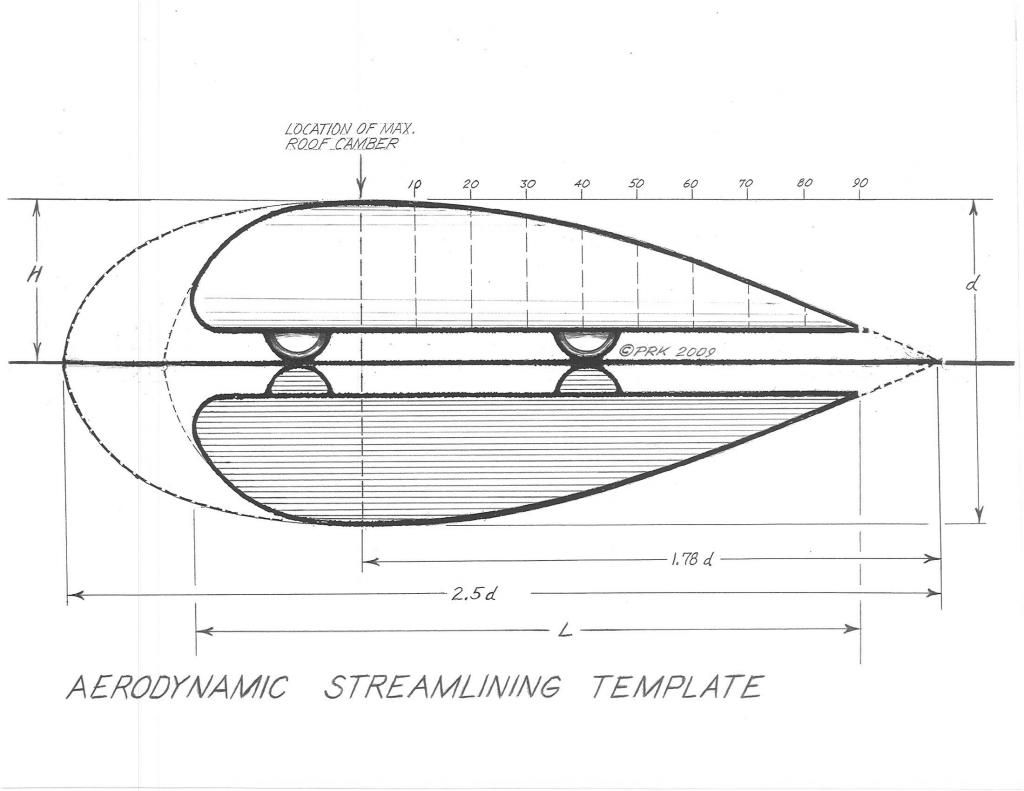
Your plan-view edges would want to follow a pathway as on the 1957 MG EX 181,with Cd 0.12.Just scale everything to the drawing.
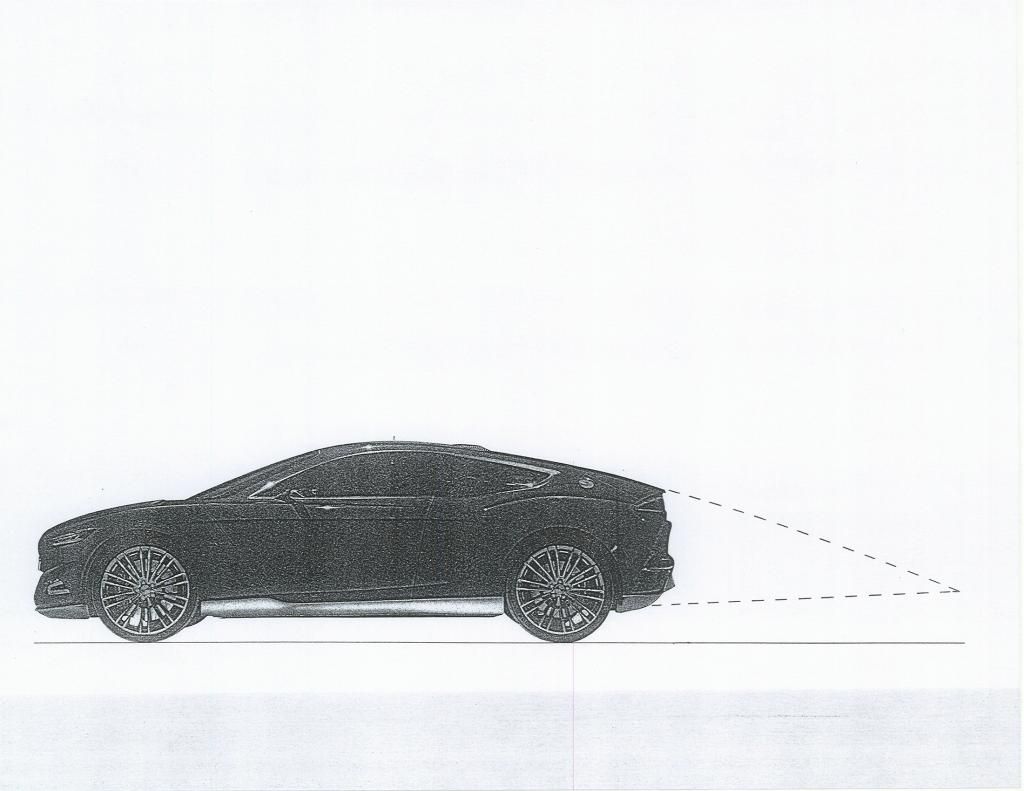
Your side panels must mimic the curvature of the SUV's body when looking from behind.
It's more work,but the air doesn't allow any shortcuts.Ever!
Here is Kamm's lowest drag K-car,Cd 0.23
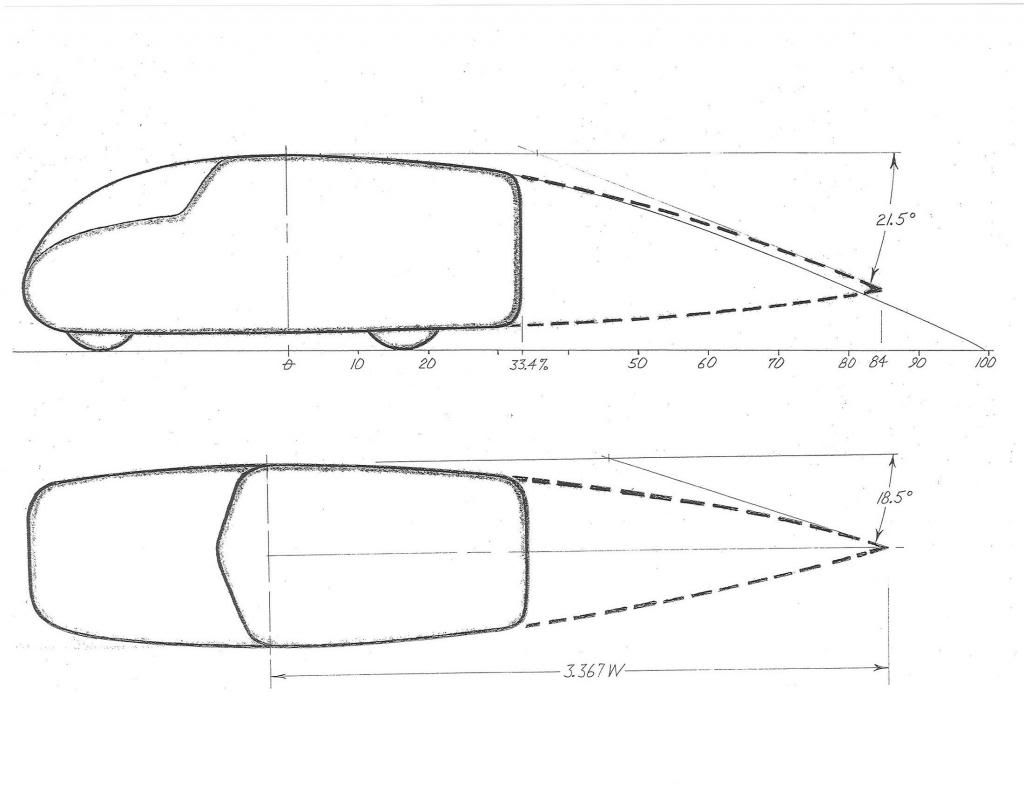
This is where you want to go. 
__________________
Photobucket album: http://s1271.photobucket.com/albums/jj622/aerohead2/
|
|
|
The Following User Says Thank You to aerohead For This Useful Post:
|
|
09-29-2014, 08:12 PM
|
#38 (permalink)
|
EcoModder In Training
Join Date: Jul 2014
Location: Cleveland, Ohio
Posts: 20
Thanks: 13
Thanked 3 Times in 2 Posts
|
Quote:
Originally Posted by freebeard
If the mileage isn't panning out, how does it feel? Any difference when you meet/pass a big truck (cattle trucks are the worst, ask aerohead)?
|
I didn't pass any big trucks during testing, and I don't know whether it was just me wanting it to be true, but the acceleration felt a little easier up to 65. I'll continue testing, then, trying to start the panels at a better spot and increase angles further, keeping attached (but turbulent) flow.
Quote:
Originally Posted by freebeard
Your vehicle already has a Kamm-back, you're wanting to return it to a partial boattail.
|
I don't understand what you mean by this. My car chops off almost parallel with the direction of motion of the car on all sides. There is little curving back inward that the sides or top do before the back cuts off. I don't think my stock car would be considered a Kammback, if that's what you mean.
Quote:
Originally Posted by freebeard
One of my favorite cars, the Volkswagen Golf GTI w12 650. The Golf is a Kamm-back, like yours, but this has been converted to a bubble-top coupe with only the skeleton of the original top left.
|
Cool car, but I'm not planning to chop or alter my stock car in any way, just add removable attachments.
Quote:
Originally Posted by freebeard
The wheel wells and underbody (diverter and difusser) offer as much opportunity as your 30% tail.
|
Underbody work will come, too; all in good time. I've been trying to go for the hardest problem first (and my hope was the biggest payoff).
__________________
"On the 8th day, God created kammbacks. And God saw that it was good."
-Genesis 1:32
|
|
|
09-29-2014, 10:44 PM
|
#39 (permalink)
|
EcoModder In Training
Join Date: Jul 2014
Location: Cleveland, Ohio
Posts: 20
Thanks: 13
Thanked 3 Times in 2 Posts
|
Quote:
Originally Posted by aerohead
You can see that it is perfectly integrated into the body with seamless transition.The air needs this 'perfection' in order to protect the boundary layer,which determined whether or not you'll have separation.
|
You all are frustratingly right.  My tail design in my head and on paper is getting increasingly complicated and more difficult to build with every time I post something and one of you makes another really great point/observation. Thanks for being frustrating.
Quote:
Originally Posted by aerohead
Your cardboard mockup is more like a box-cavity,and for it to work,it needs to be as low as the bottom of your bumpers bottom,and it needs a 'floor'.It cannot be open on the bottom unless there is a back on it,and the back is airtight.
|
I'm going to need some good clarification on this statement, as it will determine some key design choices as I move forward and piece my tail together. I understand the concept that closing the bottom would be useful to the flow from underneath the car if the sides extend to the bottom of the bumper. I understand that it would be better to extend the sides down to the bottom of the bumper so that all of the air around the car sides decelerates together and merges smoothly, not just the top half, and therefore, less turbulence. Extending down that far would significantly increase the work I need to do, though. Some questions:
1) If I don't extend the sides any further down than they already are, is a bottom still useful? If yes, please explain.
2) How does a closed back replace a closed bottom? Just to make a stagnant pocket of air that "blocks" airflow, as if it had a solid bottom panel?
3) You use the phrase "for it to work". Why wouldn't 2/3 of the kammback produce at least half, if not fully 2/3 of the benefit?
4) Would a front air dam and side skirts negate the benefit/usefulness of adding a bottom to the kammback?
__________________
"On the 8th day, God created kammbacks. And God saw that it was good."
-Genesis 1:32
Last edited by UnicycleDan; 09-29-2014 at 10:50 PM..
|
|
|
09-29-2014, 11:38 PM
|
#40 (permalink)
|
Master EcoModder
Join Date: Aug 2012
Location: northwest of normal
Posts: 28,978
Thanks: 8,225
Thanked 8,995 Times in 7,431 Posts
|
In my thinking Kamm-back is to boattail as bullet is to teardrop. Let's leave parsing Kammback from partial boattail for another time.
Questions to aerohead:
- No. I can't explain.

- Yes. aerohead saw that with his backlight in the wind tunnel.
- Yes, potentially. If it is done right.
- The front air dam and side skirts would have to reach the ground for this to be a yes.
Given the ride height of your vehicle, you might want to go with a smooth bellypan and spatted and skirted wheels. The air moving underneath would like the rear difusser better. Have a look at this design concept from Coventry University:
Even though they hold the sides in, starting as the body reaches it's max camber to leave the tail-lights exposed; look at how much the extended the top onto the existing roofline when they had the opportunity. No high mounted 3rd brakelight, apparently. They box in the bottom but there is a step rather than a difusser.
|
|
|
|