05-30-2011, 10:05 PM
|
#1 (permalink)
|
ecowannabe
Join Date: Feb 2010
Location: San Diego, CA
Posts: 64
Thanks: 2
Thanked 1 Time in 1 Post
|
Fiberglass Aeromods?
Hello all, been wanting to do some Aeromods to my 89 ford escort for a while now. I eventually want to paint the vehicle and would love to make the Aeromods permanent and out of fiberglass and then paint the car so they would blend in.
I was wondering if there were any tutorials on making custom panels with fiberglass. I have never used fiberglass but I am pretty good with my hands so I would love to try
Thanks!
Josh
|
|
|
Today
|
|
|
Other popular topics in this forum...
|
|
|
05-30-2011, 10:32 PM
|
#2 (permalink)
|
recently enlightened...
Join Date: May 2011
Location: Alberta, Canada
Posts: 55
Thanks: 12
Thanked 12 Times in 7 Posts
|
Hi !
I don't think there are any tutorials on here, I'd have to refer you to fiberglassforums.com for that. It's not too complicated; if you can cook something simple, you can do fiberglassing. There are basically just three ingredients. If you put too much hardener in the resin you lose that batch pretty quickly, and if you don't put enough, it takes longer to cure, so you can't screw anything up, you just readjust the next time.
Try this "tutorial" to give you a good idea.
The best way to do mods in fiberglass would be to start by making a "plug" (basically the shape you want but made out of cardboard, duct tape and body filler). Then by laying fiberglass on that part you make a mold. Then using your mold, you make your final part.
And something I can't stress enough, you need good protective equipement, especially a respirator and a long sleeve shirt when you're sanding. I hope this helps, someone else can chime in to add more tips. 
|
|
|
05-30-2011, 10:36 PM
|
#3 (permalink)
|
Master EcoModder
Join Date: Feb 2011
Location: Phillips, WI
Posts: 1,018
Thanks: 192
Thanked 467 Times in 287 Posts
|
Google moldless composite construction for another approach.
|
|
|
05-30-2011, 10:44 PM
|
#4 (permalink)
|
recently enlightened...
Join Date: May 2011
Location: Alberta, Canada
Posts: 55
Thanks: 12
Thanked 12 Times in 7 Posts
|
|
|
|
05-31-2011, 04:58 PM
|
#5 (permalink)
|
Master EcoModder
Join Date: Mar 2009
Location: Tustin, CA
Posts: 929
Thanks: 368
Thanked 380 Times in 238 Posts
|
Simply type in "how to fiberglass" into youtube, there will be a bunch of results.
|
|
|
06-01-2011, 01:46 PM
|
#6 (permalink)
|
ecowannabe
Join Date: Feb 2010
Location: San Diego, CA
Posts: 64
Thanks: 2
Thanked 1 Time in 1 Post
|
Thanks for the info! 
Im thinking dropping front bumper down, wheel skirts (back and I'd like to do front too) and a kammback (trying to figure out a way to not block the view out the window) oh and a grill block (i'd like to taper the hood to the front bumper)
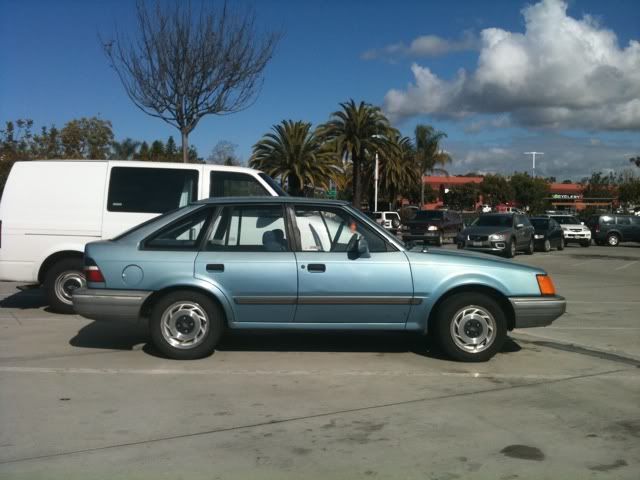
|
|
|
06-03-2011, 04:19 PM
|
#7 (permalink)
|
ecowannabe
Join Date: Feb 2010
Location: San Diego, CA
Posts: 64
Thanks: 2
Thanked 1 Time in 1 Post
|
How much do you think my Cd could be improved? I havent found it on the net or calculated it yet tho
|
|
|
06-03-2011, 06:05 PM
|
#8 (permalink)
|
Master EcoModder
Join Date: Jan 2008
Location: Sanger,Texas,U.S.A.
Posts: 16,404
Thanks: 24,471
Thanked 7,410 Times in 4,800 Posts
|
Cd 0.24?
Quote:
Originally Posted by jmedia
How much do you think my Cd could be improved? I havent found it on the net or calculated it yet tho
|
My CRX started around Cd 0.35 and 52 mpg at a constant 55 mph.Top speed-93 mph
My mods:
* a modest nose fascia to cover the existing nose ( 6-inches depth with grille block,radiused inlet duct,Plex. covered fenestrations for turn signals )
* lower front airdam
* rocker panel extensions to 'bottom' of underside
* bellypan with 2.5-degree diffuser
* front wheel gap-fillers
* MOON style wheel covers
* Full rear wheel skirts
* Rear hatch header buttress extensions with Backlight top wing
* 1-foot slip-on boat tail
-------------------------------------------------------------------------
Modified drag coefficient: Cd 0.235.
60 + mpg @ 55 mph
Top speed - 100 mph
--------------------------------------------------------------------------
I think you could certainly get to the same numbers on Cd.You have more frontal area so your CdA is higher,but still,a 28% mpg increase at least.
|
|
|
07-22-2011, 04:15 AM
|
#9 (permalink)
|
EcoModding Lurker
Join Date: Jul 2011
Location: ca
Posts: 24
Thanks: 0
Thanked 6 Times in 5 Posts
|
I don't quite know how to tell you it's easy & hard at the same time. I wish I could tell you everything about it in a nut shell. Knowing the terminology for the materials, tools & process is fundamental. As an example, the hardener for polyester resin (which most people call fiberglass resin) is MEKP. Unfortunately, in my opinion, polyester resin is often mis-labeled on the cans, as fiberglass resin. Also (& I'm not trying to nit pick here), but if you were looking for MEK peroxide you may end up with something else. MEK, by itself, is a completely different chemical, and would not harder polyester resin. MEKP( Methyl Ethel Keytone Peroxide) needs to be added to the resin in a very specific %, depending on the temp & humidity.Testing is always a good idea I still use the same triple beam metric scale that my brother & I used back in the 70s, when we made fiberglass parts. There are 2 kinds of polyester. Tooling resin & just regular resin. I won't go into all the chemistry. You don't need tooling resin. What few people know is that the chemical that you smell, with polyester, is called Styrene. It's the thinner, and can be purchased separate and added in small amounts for certain things. If you did a lot of work with resin, you would probably want some around. Another resin, that is close in similarity to polyester is called Vinylester resin. It has similar properties, but can be used in applications for use with other chemical storage. Epoxy resin is way different, for the exception of the combination causes the same heat process called 'exotherm'. You will find, if you get into a conversation with people who are selling the products, you'll be on the same page about the products & processes. There are dozens of little things, and chemicals, that are helpful in making the process of fabrication of molds & parts quite easy. And unbelievably hard, if you don't. I actually want to do a real pro looking aero mold group, kit if you will, for a honda or metro. Getting back on subject here, I read thru some of the links that had been posted to read & found most of the info was correct, for the exception of how many layers of material was needed. That will entirely be dependent on the weight of the material you choose to work with. I'll agree that using cloth, even light cloth, will produce a pattern called 'print through' and will have much more satisfactory results with 'random mat'. When you have honed your skills, you should be using just about the same weight of both glass & resin. Maybe just a touch more resin, otherwise you will be 'resin rich', which makes the piece weigh more & be a little less strong. Having the right tools is very handy, and are sold be the people who sell the materials. I would recommend using Kevlar for your mounting points. You'll need good scissors for that. You are much better off finding a place you can 'walk in' to purchase, because of shipping penalties you pay for chemicals. Sometimes it adds $100s to the bill. Look up composite materials & you should come up with lots of suppliers. I use Fiberglass Hawaii, in Ventura, Ca. By the way, West System is the most common Epoxy and a great product. Shop around for the best price.
I wish you the best of luck on your project. Try to make it fun. It will be a terrific learning process, that will be very rewarding and helpful on your future projects. If you need any questions asked, I'll try to help the best I can.
|
|
|
|