04-04-2015, 11:16 PM
|
#61 (permalink)
|
Master EcoModder
Join Date: Oct 2009
Location: Red Deer, AB
Posts: 421
Thanks: 39
Thanked 96 Times in 69 Posts
|
I should also say your conversions are very impressive. Your attention to detail is incredible .
__________________
Almost all my driving is done 1-5 miles at a time.
Best short trip: 2.4 l/100 km, 3.9 km
|
|
|
Today
|
|
|
Other popular topics in this forum...
|
|
|
04-05-2015, 09:09 PM
|
#62 (permalink)
|
EcoModding Apprentice
Join Date: Feb 2015
Location: Sacramento
Posts: 202
Thanks: 3
Thanked 225 Times in 91 Posts
|
Quote:
Originally Posted by puddleglum
I have a few questions about your battery choice. Have you used any of your conversions long enough to have any idea of how reliable these cells are? Have you had any faulty ones? Also, how do they compare in price to CALB or Winston for example. Do you order them straight from China and, if so, have they been good to deal with?
|
I don't have long term data yet, but I have lotsa real world experience with these batteries. I imported them myself from China, and am pretty happy with them so far. I did have one that was sick in the pack in my second conversion, and the manufacturer had a replacement air mailed, and on my doorstep, no expense to me, within a few days. I have not used calb or winston cells, so I am not sure how they compare. I have a pack of GBS batteries in my first conversion, and I am not as happy with those ones as I am with these. Those GBS batteries have not given me any trouble, but they do sag a little more under load.
|
|
|
01-08-2016, 06:29 PM
|
#63 (permalink)
|
EcoModding Apprentice
Join Date: Feb 2015
Location: Sacramento
Posts: 202
Thanks: 3
Thanked 225 Times in 91 Posts
|
I have been running a 4.39 transmission in this rig, but am getting ready to put a 3.79 in here. I got hold of a 3.52 ring and pinion and am building a 3.52 transmission with it for my first conversion, so the 3.79 that I was running in that rig will be available to put into this EV
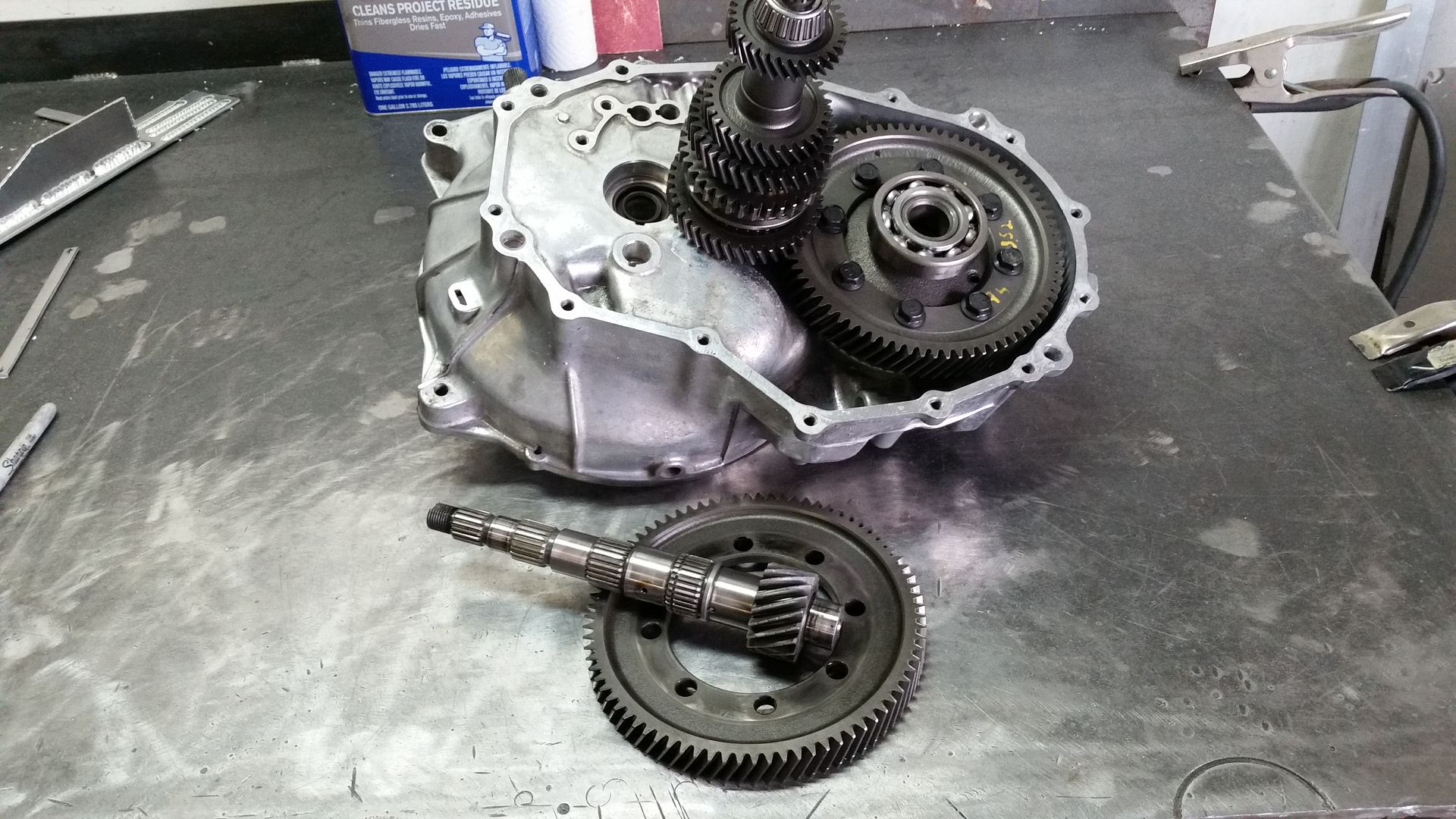 .
|
|
|
01-08-2016, 07:49 PM
|
#64 (permalink)
|
...beats walking...
Join Date: Jul 2009
Location: .
Posts: 6,190
Thanks: 179
Thanked 1,525 Times in 1,126 Posts
|
Curiosity question: how "low" final gearing do think is possible (for your conversion) before it becomes "too much" and motor lugging becomes a problem...assuming it's NOT being driven up Pike's Peak.
|
|
|
01-08-2016, 08:38 PM
|
#65 (permalink)
|
EcoModding Apprentice
Join Date: Feb 2015
Location: Sacramento
Posts: 202
Thanks: 3
Thanked 225 Times in 91 Posts
|
Quote:
Originally Posted by Old Tele man
Curiosity question: how "low" final gearing do think is possible (for your conversion) before it becomes "too much" and motor lugging becomes a problem...assuming it's NOT being driven up Pike's Peak.
|
Since there 5 gears to choose from, it never really becomes too much, it is just a matter of driver preference. With the huge amount of torque available and a torque curve that drops off sharply after 3200 rpm, I like to enjoy that limited torque band for a longer duration before having to go for another gear. I often just put it in fourth and never shift all the way home at night, but sometimes I will launch in 3rd so I can get a more satisfying blast of torque. I don't even bother with 1st or 2nd, but maybe 2nd will be of more interest with the new 3.52 ratio. I only use 5th on the freeway, and am looking forward to a little boost in available torque at high speeds. I often take it above 80 mph, but that is where the torque falls off, so it is not as exciting at those higher speeds.
Just realized that this is the third conversion thread, not the first conversion thread, so my response is off a little. The same applies, but even more so, since it is a bigger jump from a 439 to a 379. This rig has a bit less torque, but it will still be a big improvement.
Last edited by EVmetro; 01-08-2016 at 11:37 PM..
|
|
|
The Following User Says Thank You to EVmetro For This Useful Post:
|
|
01-09-2016, 02:54 PM
|
#66 (permalink)
|
...beats walking...
Join Date: Jul 2009
Location: .
Posts: 6,190
Thanks: 179
Thanked 1,525 Times in 1,126 Posts
|
I'm a retired EE and well aware that (typically) a series DC-motor produces it's greatest torque at zero-rpm, but that's not how parallel AC-motors work, so was wondering what your "design" goal was for changing gearing ratios.
Like I said, merely a curiosity question.
|
|
|
01-09-2016, 04:28 PM
|
#67 (permalink)
|
EcoModding Apprentice
Join Date: Feb 2015
Location: Sacramento
Posts: 202
Thanks: 3
Thanked 225 Times in 91 Posts
|
Quote:
Originally Posted by Old Tele man
I'm a retired EE and well aware that (typically) a series DC-motor produces it's greatest torque at zero-rpm, but that's not how parallel AC-motors work, so was wondering what your "design" goal was for changing gearing ratios.
Like I said, merely a curiosity question.
|
I welcome questions and discussion. My formal education goes to 3 years of high school, but I do enjoy DIY EV discussion with EE types. This particular build is the result of what I learned from a couple earlier builds, plus a lot of studying of thermodynamics.
The goals of the gearing changes are to maintain the most efficiency, but also to offer better driving options. While the eco driving efficiency is astonishing, I also like to run the left lane and run it really hard. Changing the gearing won't change anything as far as efficiency goes, but it will cover a broader range of driving styles.
I have the throttle mapped with a time delay, but also progressively more power as the rpms rise. In my second conversion, I have 1200 amps and 144 volts available to my DC motor all at once, and it is really fun, but on this rig the throttle mapping is set up for a really easy to drive experience. I have an eco mode switch on the dash that allows me to reconfigure my power, regen, and throttle settings with a flip of a switch, so I can select between ultimate efficiency or performance. Since my HVDC circuit is only 115 volts, the five speed transmission with the 3.79 gearing will cover the narrower rpm band better for both types of driving.
|
|
|
01-09-2016, 06:38 PM
|
#68 (permalink)
|
Master EcoModder
Join Date: Sep 2010
Location: Saskatoon, canada
Posts: 1,488
Thanks: 746
Thanked 565 Times in 447 Posts
|
Quote:
Originally Posted by Old Tele man
I'm a retired EE and well aware that (typically) a series DC-motor produces it's greatest torque at zero-rpm, but that's not how parallel AC-motors work, so was wondering what your "design" goal was for changing gearing ratios.
Like I said, merely a curiosity question.
|
Did I miss something? Parallel AC motors? I saw a picture of a single AC35 early on ...
Does this refer to another thread?
|
|
|
01-09-2016, 08:19 PM
|
#69 (permalink)
|
...beats walking...
Join Date: Jul 2009
Location: .
Posts: 6,190
Thanks: 179
Thanked 1,525 Times in 1,126 Posts
|
Most AC-motors are multi-phase (ie: 3-phase) because they *work* using rotating magnetic fields (plural = phases)...whereas DC-motors typically use only a single winding (but CAN actually have multiple windings) and thus are only 'single' phased.
It was only meant to clarify the fact that "...maximum torque at low speed..." is a hallmark of DC-motors, but not so of AC-motors.
|
|
|
01-09-2016, 11:47 PM
|
#70 (permalink)
|
Master EcoModder
Join Date: Sep 2010
Location: Saskatoon, canada
Posts: 1,488
Thanks: 746
Thanked 565 Times in 447 Posts
|
Quote:
Originally Posted by Old Tele man
Most AC-motors are multi-phase (ie: 3-phase) because they *work* using rotating magnetic fields (plural = phases)...whereas DC-motors typically use only a single winding (but CAN actually have multiple windings) and thus are only 'single' phased.
It was only meant to clarify the fact that "...maximum torque at low speed..." is a hallmark of DC-motors, but not so of AC-motors.
|
OK.
The Torque/Power graph here is a bit confusing to me. I, like you, would not have expected torque to peak at the lowest rpm recorded. http://www.hpevs.com/Site/power_grap...ak%20graph.pdf
HPEVS must have a rotor design quite different from a typical AC induction motor ... I have seen (at work) maybe 150 - 200% of motor rated torque at 0 rpm but it increases to maybe 250% (briefly) from about 5 or 6 Hz up to rated frequency. In the case of the AC35 I'd almost guess that 900 rpm is the rated frequency?
The AC34 curve looks more like I'd expect from an induction motor, rated for 1800 rpm. http://www.hpevs.com/Site/power_grap...ial%20peak.pdf
The AC-34 was done at 48V, so it's not a perfect comparison ..
I'd have to agree with EVMetro's assessment that having less gear reduction from the motor to the wheels would give the AC35 a higher top end and make it more fun to drive. Perhaps second gear will become more useful as well.
|
|
|
|