08-14-2013, 03:41 PM
|
#201 (permalink)
|
Batman Junior
Join Date: Nov 2007
Location: 1000 Islands, Ontario, Canada
Posts: 22,541
Thanks: 4,085
Thanked 6,989 Times in 3,619 Posts
|
Deja vu!
(PS: you're getting your fancy paint job dirty.)
|
|
|
The Following User Says Thank You to MetroMPG For This Useful Post:
|
|
Today
|
|
|
Other popular topics in this forum...
|
|
|
08-14-2013, 03:45 PM
|
#202 (permalink)
|
Master EcoModder
Join Date: Jul 2008
Location: Langley, BC
Posts: 1,228
Fusion - '16 Ford Fusion Hybrid SE
Thanks: 190
Thanked 275 Times in 168 Posts
|
Quote:
Originally Posted by MetroMPG
Deja vu!
|
Yeah, it's a like a Forkenswift rerun, 6 years later!
Quote:
(PS: you're getting your fancy paint job dirty.)
|
I know! It probably doesn't matter, considering it will be hidden underneath the front battery pack anyway.... 
|
|
|
08-14-2013, 03:51 PM
|
#203 (permalink)
|
Administrator
Join Date: Dec 2007
Location: Germantown, WI
Posts: 11,203
Thanks: 2,501
Thanked 2,590 Times in 1,556 Posts
|
Don't you want to advance it a bit more since you're running a higher voltage than the motor was designed for?
|
|
|
08-14-2013, 04:04 PM
|
#204 (permalink)
|
Master EcoModder
Join Date: Jul 2008
Location: Langley, BC
Posts: 1,228
Fusion - '16 Ford Fusion Hybrid SE
Thanks: 190
Thanked 275 Times in 168 Posts
|
Quote:
Originally Posted by Daox
Don't you want to advance it a bit more since you're running a higher voltage than the motor was designed for?
|
Do I? I really have no idea.
From what read on diyelectriccar.com, 12 degrees seems to be the max for EV motors like Warp 9s and stuff like that. More advance has the same effect as field weakening, so less torque and higher speed. Finding the best amount of advance for any situation is trial and error.
I was very surprised at how much advance my motor has. But for now I think I will go with what it is and then test. If the arcing is too much I will have to advance more.
|
|
|
The Following User Says Thank You to mechman600 For This Useful Post:
|
|
08-14-2013, 11:14 PM
|
#205 (permalink)
|
Master EcoModder
Join Date: Oct 2009
Location: Red Deer, AB
Posts: 421
Thanks: 39
Thanked 96 Times in 69 Posts
|
Looking really good.
__________________
Almost all my driving is done 1-5 miles at a time.
Best short trip: 2.4 l/100 km, 3.9 km
|
|
|
08-15-2013, 01:19 PM
|
#206 (permalink)
|
Master EcoModder
Join Date: Jul 2008
Location: Langley, BC
Posts: 1,228
Fusion - '16 Ford Fusion Hybrid SE
Thanks: 190
Thanked 275 Times in 168 Posts
|
I got the motor back together yesterday and powered it up. Now it spins the right direction, so that's a good thing! It also seems to spin a bit faster than before (going by the pitch of the sound it makes). I don't know if this is because the battery cart was low on charge the first time I powered the motor (we use it to jump start Peterbilts) or if my brush timing is a bit off. The speeds seem to be very close, so I will leave it for now. You can hear the difference in the before and after videos.
Before:
After rotation and brush timing change:
The second one is much louder because the motor is running with the brush end up, as opposed to down in the first video.
|
|
|
08-18-2013, 02:18 AM
|
#207 (permalink)
|
Master EcoModder
Join Date: Jul 2008
Location: Langley, BC
Posts: 1,228
Fusion - '16 Ford Fusion Hybrid SE
Thanks: 190
Thanked 275 Times in 168 Posts
|
Yesterday I removed the motor from the Electric Booger. It was like removing a starter from a Peterbilt. Took a grand total of 50 minutes, which included dismantling and removing the front battery pack.
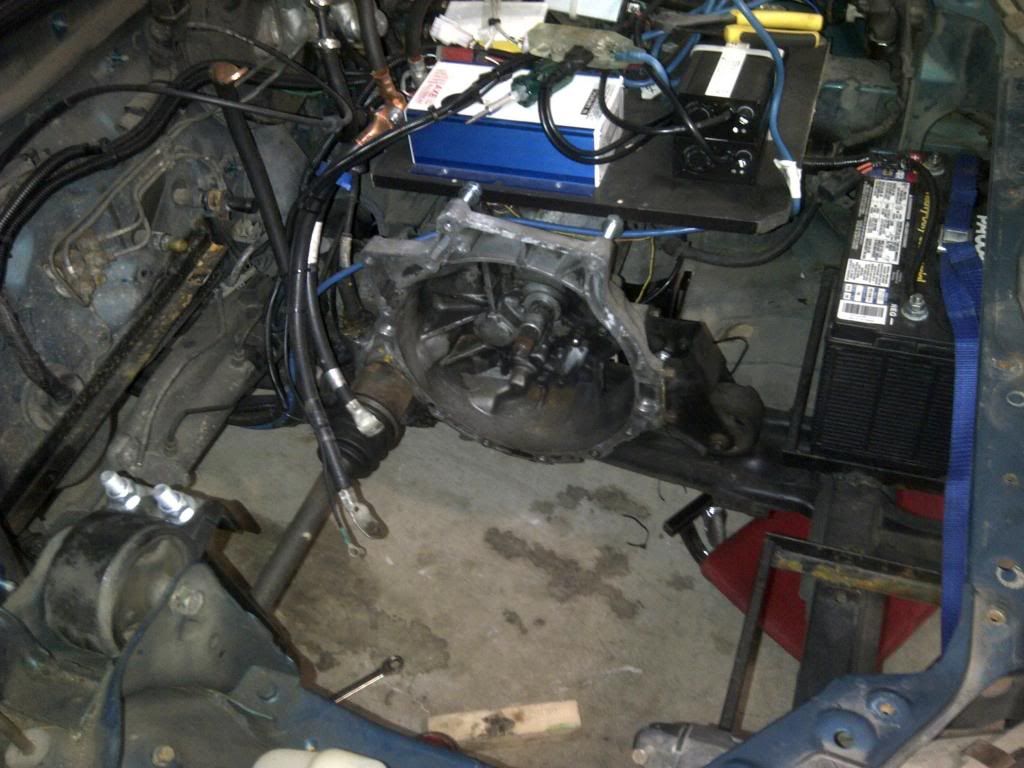
I took the opportunity to inspect my coupler. There is no way to get at my coupler when the motor is installed, so I was going on faith that it was still good. Close inspection reveals no noticeable wear after 1200 miles.
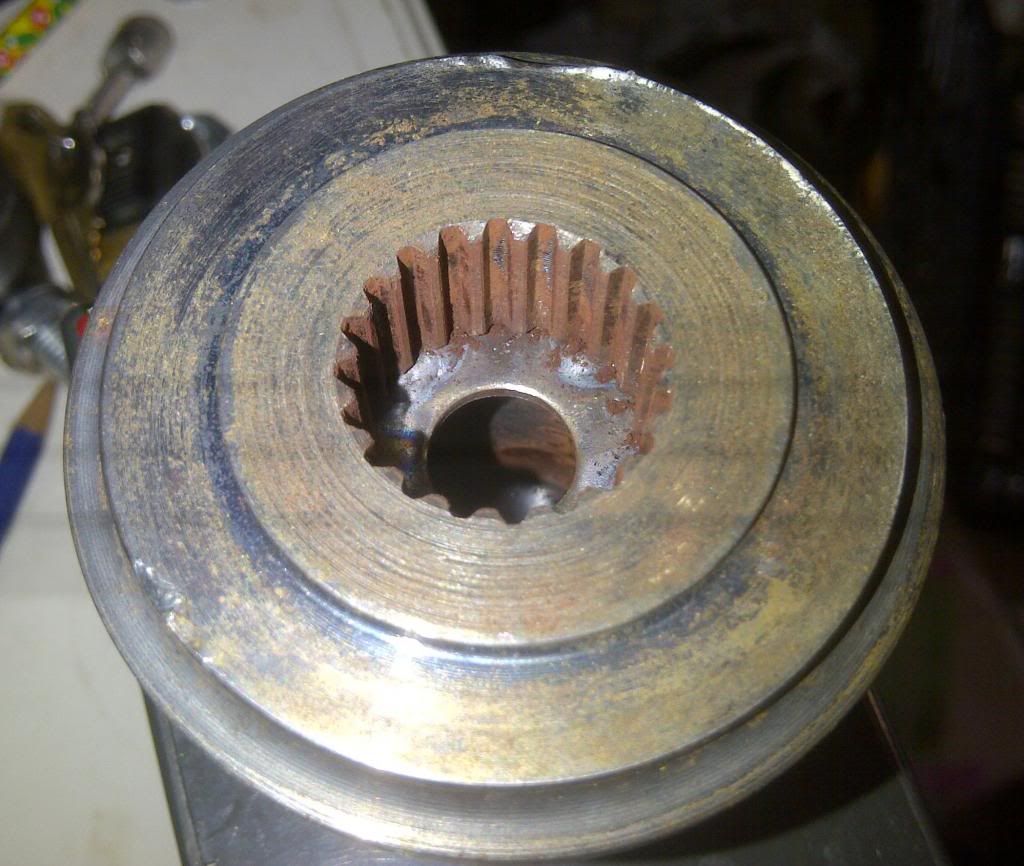
Maybe a bit rusty, so I will definitely put some grease in there this time.
I scribed a line around the old sepex motor before removing it from the adapter plate. I then gave the adapter plate and drive end cap from the new motor to my machinist buddy to drill and mount. I don't trust myself with this one.
Today I messed around with something I should have done right from the beginning: grille blocks. Here they are, made from the same chunk of plexiglass that covers my rear battery pack:
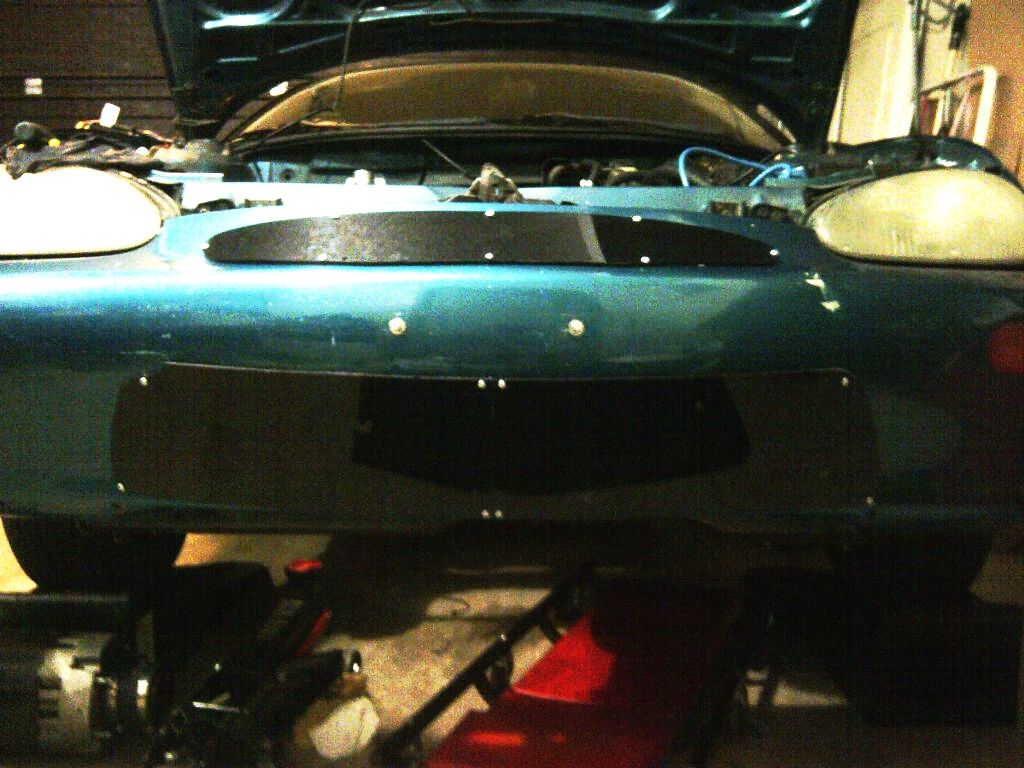
Contrary to popular belief, these ones are not for aerodynamics (although they may help me beat my top speed record of 60 mph). Instead they are meant to keep the rain off the front batteries, whose connections get corroded up pretty fast.
|
|
|
08-19-2013, 12:11 AM
|
#208 (permalink)
|
Master EcoModder
Join Date: Dec 2010
Location: Crescent City, CA
Posts: 285
Thanks: 17
Thanked 39 Times in 22 Posts
|
Always like the MX-3 design. Looks pretty aero. Wanted to do a RF diesel conversion in one of these. Unfortunately though, after my recent move, it left me without garage space : /
VT247
|
|
|
08-19-2013, 01:08 PM
|
#209 (permalink)
|
Batman Junior
Join Date: Nov 2007
Location: 1000 Islands, Ontario, Canada
Posts: 22,541
Thanks: 4,085
Thanked 6,989 Times in 3,619 Posts
|
Quote:
Originally Posted by mechman600
I then gave the adapter plate and drive end cap from the new motor to my machinist buddy to drill and mount. I don't trust myself with this one.
|
Same here!
|
|
|
08-22-2013, 05:16 AM
|
#210 (permalink)
|
Master EcoModder
Join Date: Jul 2008
Location: Langley, BC
Posts: 1,228
Fusion - '16 Ford Fusion Hybrid SE
Thanks: 190
Thanked 275 Times in 168 Posts
|
Tachometer Success!
Part of the plan here is to get the tachometer working. Although I don't REALLY need it, it would be cool to have. Currently the only gauge that works is my speedometer, which is lame.
Today I had a breakthrough. My friend Matt (the machinist) gave me a proximity sensor, which is basically a switch that turns on when metal is nearby.
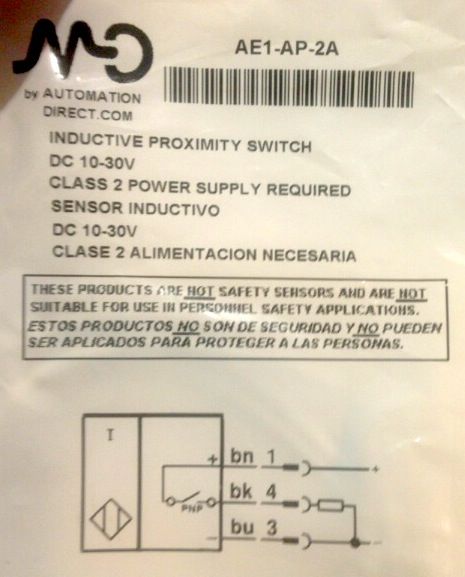
My tachometer was originally fed a signal from the negative side of the ignition coil (which is the norm). I wired the proximity sensor this way to achieve a similar signal:
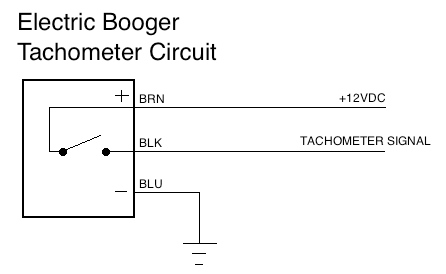
Since this was a four cylinder, with four engine position teeth in the distributor turning at half engine speed, I planned to put two pickup teeth on my drive coupler. Here is my wild setup to test it out:
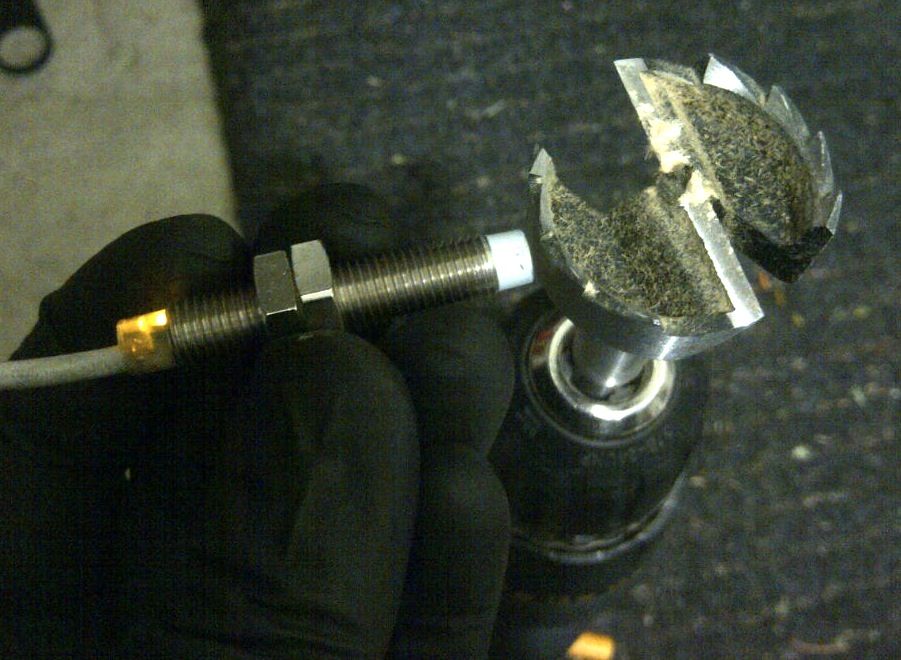
A cordless drill with a hole cutting bit with two cutouts. In theory, my tach should accurately tell me the speed of my drill. So with a fully charged battery in the drill I let 'er rip. The drill says 0-1300 RPM on it, and my tach showed 1200 RPM.
CLOSE ENOUGH!
Last edited by mechman600; 08-22-2013 at 05:31 AM..
|
|
|
|