08-02-2013, 11:53 PM
|
#191 (permalink)
|
Master EcoModder
Join Date: Jul 2008
Location: Langley, BC
Posts: 1,228
Fusion - '16 Ford Fusion Hybrid SE
Thanks: 190
Thanked 275 Times in 168 Posts
|
New motor
She arrived on a pallet this morning. I was very quick to give 'er some power and see what happened:
It spins much much faster than my sepex motor does unloaded, but series wound motors do that because of built in field weakening (something most DIY EVers take for granted!). And it spins backwards. Since it only has two power studs, this will require rewiring some of the internals to reverse the polarity between the armature and field. For those who have read the Forkenswift build thread, this may turn into a giant rerun of that. But reruns are cool once in a while, no?
Another concern is the tiny internal splines on the drive end. Check out how tiny they actually are:
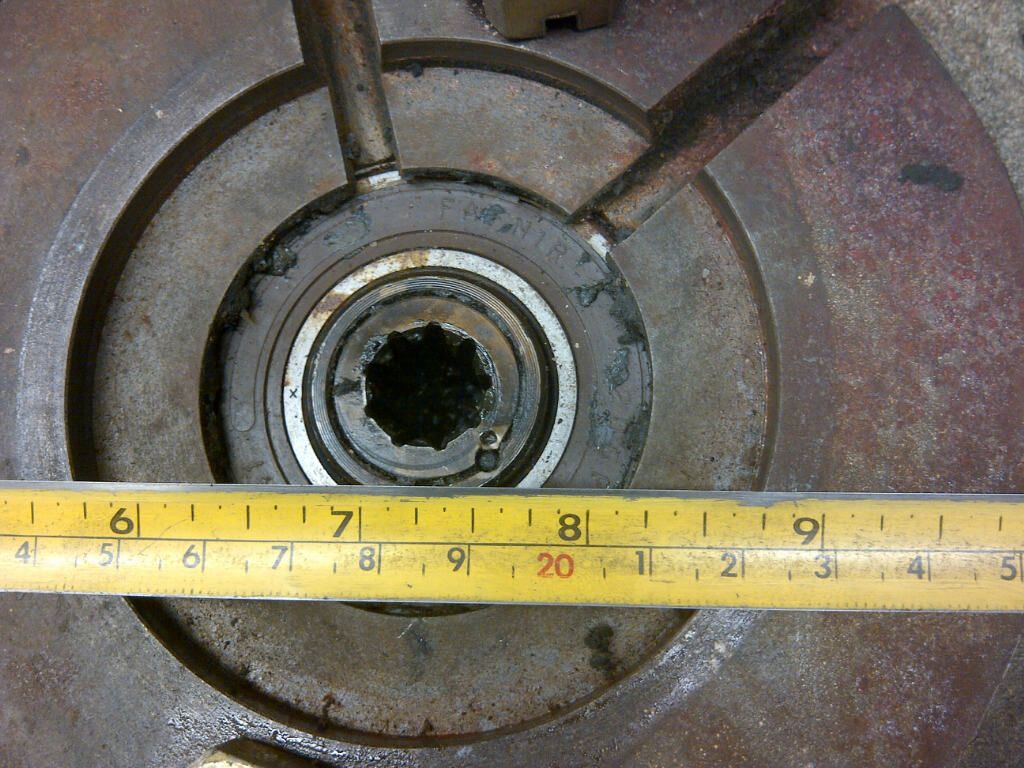
The mating shaft is about 1/2" diameter at its smallest point. According to all my research, 50 ft/lbs of torque requires a shaft diameter of 0.55", so this would be iffy at best.
I wonder if I should take the armature to my machinist and get him to install a shaft. That would be stronger and wouldn't require a new coupler. 
|
|
|
Today
|
|
|
Other popular topics in this forum...
|
|
|
08-03-2013, 01:02 PM
|
#192 (permalink)
|
Master EcoModder
Join Date: Jul 2008
Location: Langley, BC
Posts: 1,228
Fusion - '16 Ford Fusion Hybrid SE
Thanks: 190
Thanked 275 Times in 168 Posts
|
She almost let me down....
On Thursday's commute home, my CD player kept cutting out on me.
"I guess that's normal for a 20 year old 10-disk changer playing a burned CD", I thought. (What's a CD, anyway??).
Yesterday morning it did it again. I wasn't too concerned until I realized it was happening with each application of the brakes. Huh? I pulled up to the next stop sign and heard a low drone of a vacuum pump ("bwaaaahhhh") instead of an eager hum ("bweeeeeeh") and realized that my accessory battery was pretty much dead. Not too concerning until I remembered that this battery powers the main contactor.
Well, I made it to work without a hitch. And I charged that battery all day long with a real battery charger (it consumed a lot of current). I think it has been falling behind the main pack due to my shortened summer charging events (the more efficient warmer temps require shorter charging times). Also, my four year old plays in the car often and leaves interior lights on and whatnot. Yeah, that'll do it. 
|
|
|
08-04-2013, 03:32 PM
|
#193 (permalink)
|
Batman Junior
Join Date: Nov 2007
Location: 1000 Islands, Ontario, Canada
Posts: 22,534
Thanks: 4,082
Thanked 6,979 Times in 3,614 Posts
|
I've had that happen before too (12v & main contactor). I always carry a jumper though, so I can drive with no accessory battery (or lights, signals, ...)
---
Glad the motor arrived!
Quote:
Originally Posted by mechman600
Another concern is the tiny internal splines on the drive end. Check out how tiny they actually are:
I wonder if I should take the armature to my machinist and get him to install a shaft. That would be stronger and wouldn't require a new coupler. 
|
I remember going through the same thought process, minus the actual research. If it's any consolation, the wee shaft has not yet twisted off as a result of the ForkenSwift's massive torque.
But a beefy new shaft would be nice. It's too bad there were no tailshafts on these motors, because we could have just used those.
|
|
|
08-05-2013, 03:12 AM
|
#194 (permalink)
|
Master EcoModder
Join Date: Jul 2008
Location: Langley, BC
Posts: 1,228
Fusion - '16 Ford Fusion Hybrid SE
Thanks: 190
Thanked 275 Times in 168 Posts
|
Quote:
Originally Posted by MetroMPG
If it's any consolation, the wee shaft has not yet twisted off as a result of the ForkenSwift's massive torque.
|
How many amps is your current (PUN!) controller? As amps is proportional to torque, it would be good to know.
Yesterday I stripped the motor down:
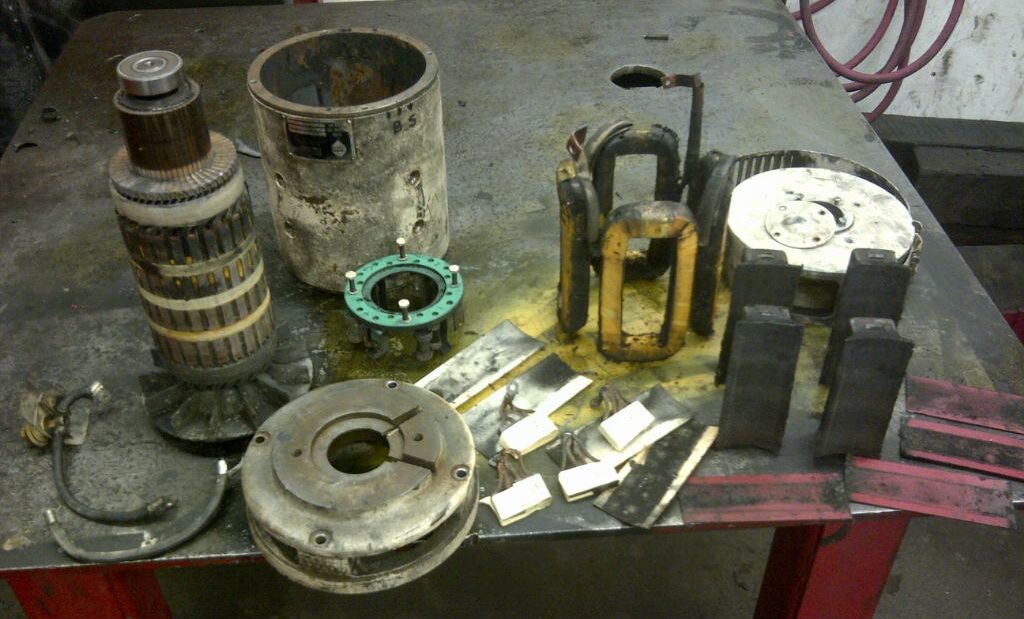
Man was it ever full of disgusting guk! After a good cleaning, it looks like this motor is in very good condition.
Field windings:
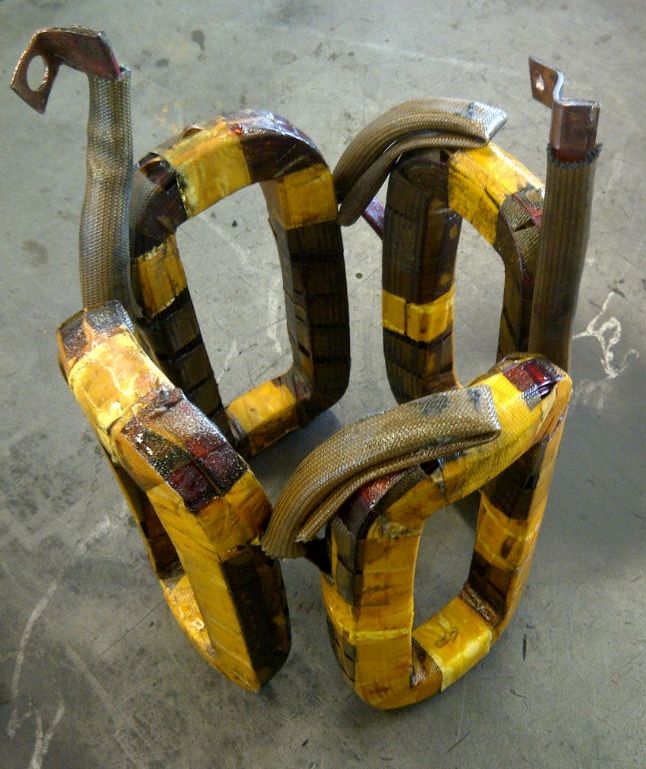
Armature:
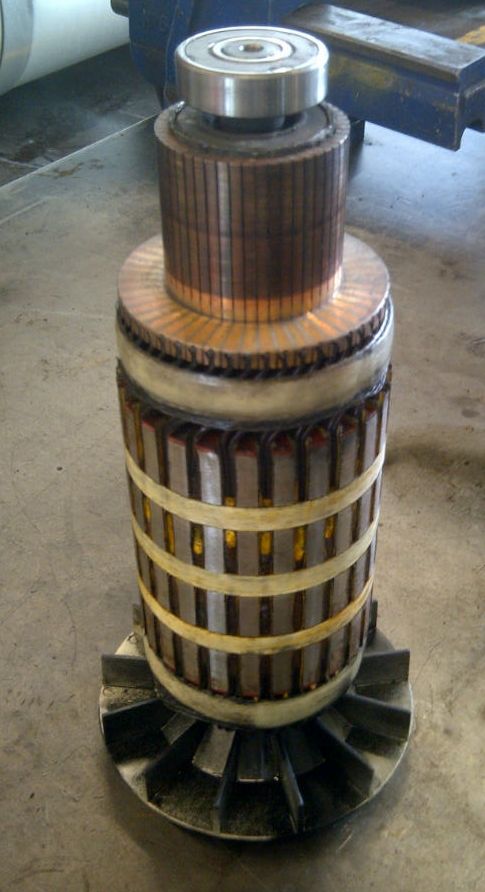
Brush holder:
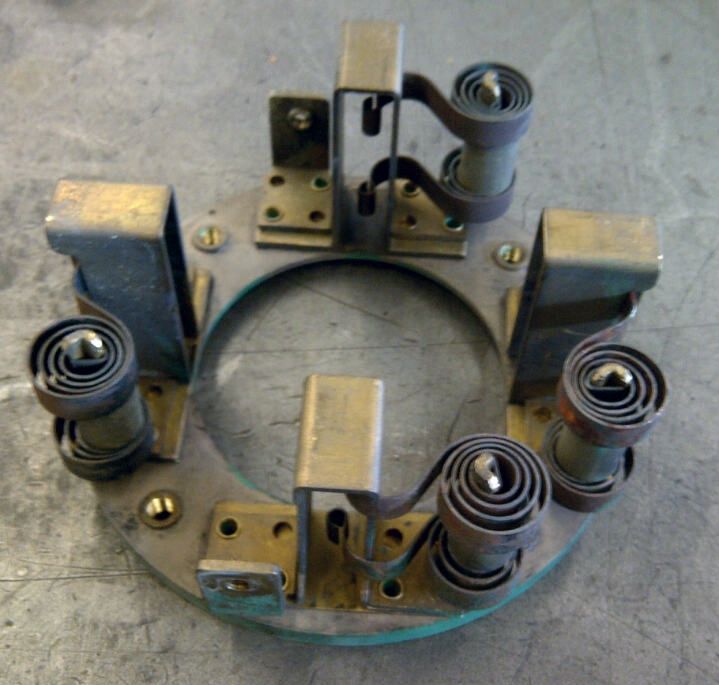
Field coils/shoes installed in the case:
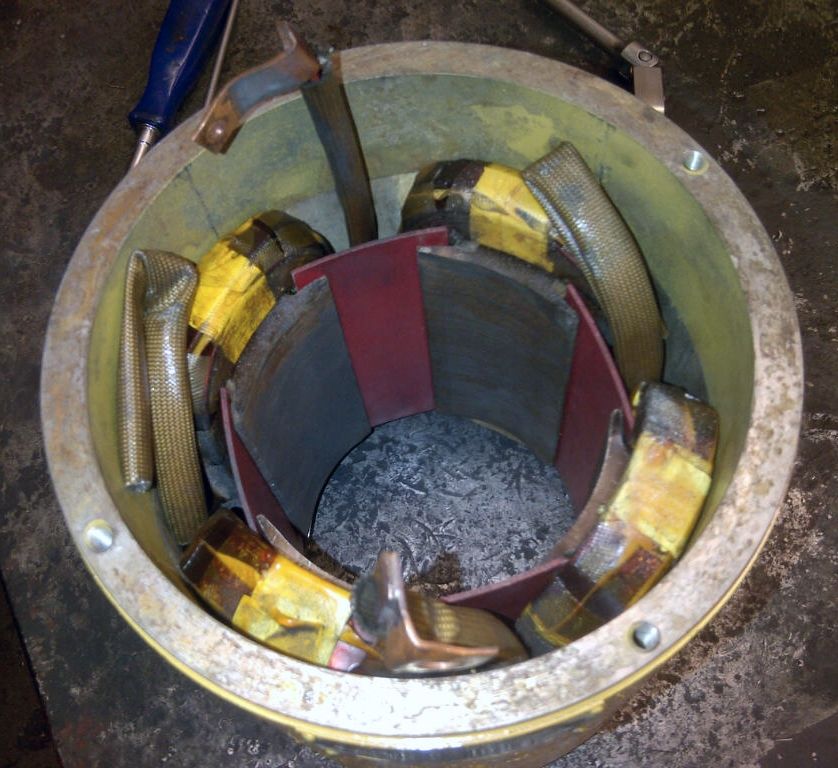
Here is what happens when you find a can of Caterpillar yellow paint laying around:

Even if it doesn't work, it sure will be pretty! 
|
|
|
08-05-2013, 08:26 AM
|
#195 (permalink)
|
Batman Junior
Join Date: Nov 2007
Location: 1000 Islands, Ontario, Canada
Posts: 22,534
Thanks: 4,082
Thanked 6,979 Times in 3,614 Posts
|
Oooo... looks nice!
Controller amps are 400. Voltage: 48. Math... up to you!
Edit... as an aside, thet twin motor in the ForkenSwift has never gotten hot. Extra toasty warm? Sure. But never so warm that I couldn't leave my hand on it, even after an extended (20-25 minute) run at ultimate maximum top speed (~65 km/h on the flat).
|
|
|
08-05-2013, 10:21 AM
|
#196 (permalink)
|
Master EcoModder
Join Date: Jul 2008
Location: Langley, BC
Posts: 1,228
Fusion - '16 Ford Fusion Hybrid SE
Thanks: 190
Thanked 275 Times in 168 Posts
|
Quote:
Originally Posted by MetroMPG
Oooo... looks nice!
Controller amps are 400. Voltage: 48. Math... up to you!
Edit... as an aside, thet twin motor in the ForkenSwift has never gotten hot. Extra toasty warm? Sure. But never so warm that I couldn't leave my hand on it, even after an extended (20-25 minute) run at ultimate maximum top speed (~65 km/h on the flat).
|
Now I am delighted.
The math is simple, really. My 450 amp Alltrax controller outputs 12.5% more amps than your Curtis, which means roughly 12.5% more torque, minus slightly more efficiency loss with the higher current. The big difference is that my 72 volts can jam those amps in a much higher RPM than yours, meaning more HP.
Wow...here I am sounding like the Electric Booger is a high performance machine of some sort!
The fan seems really powerful on this motor. It's the main thing you hear when it's running. It will be interesting to see how it handles the hill on the way home from work.
One thing I am doing this time is drilling and tapping the case/end cap somewhere to install the coolant temp sensor from the ICE. I kept it for such an occasion. Though it won't be accurate (as OEM temp gauges never are), at least it will be somewhat functional.
|
|
|
08-09-2013, 03:11 AM
|
#197 (permalink)
|
Master EcoModder
Join Date: Oct 2009
Location: Red Deer, AB
Posts: 421
Thanks: 39
Thanked 96 Times in 69 Posts
|
I don't think your coolant sensor will work right since they are designed to be submersed in coolant.
__________________
Almost all my driving is done 1-5 miles at a time.
Best short trip: 2.4 l/100 km, 3.9 km
|
|
|
08-09-2013, 10:27 AM
|
#198 (permalink)
|
Master EcoModder
Join Date: Jul 2008
Location: Langley, BC
Posts: 1,228
Fusion - '16 Ford Fusion Hybrid SE
Thanks: 190
Thanked 275 Times in 168 Posts
|
Quote:
Originally Posted by puddleglum
I don't think your coolant sensor will work right since they are designed to be submersed in coolant.
|
I have used them to measure air temp before and they work fine.
|
|
|
08-13-2013, 06:54 PM
|
#199 (permalink)
|
Master EcoModder
Join Date: Jul 2008
Location: Langley, BC
Posts: 1,228
Fusion - '16 Ford Fusion Hybrid SE
Thanks: 190
Thanked 275 Times in 168 Posts
|
You can scratch #7 off my TO DO list (TPS potentiometer). The wonky pot was making the car very very jerky at small throttle inputs, and only after sitting for a day or two. If I pumped the pedal a few times before turning the key switch on, it was okay.
The other day I found a can of Wurth electrical contact cleaner laying around, so I sprayed a crap load of it into the small holes in the pot box and down the pot shaft, hoping that some would get inside the contacts.
Wouldn't you know it: it's perfect now.
|
|
|
08-14-2013, 04:38 PM
|
#200 (permalink)
|
Master EcoModder
Join Date: Jul 2008
Location: Langley, BC
Posts: 1,228
Fusion - '16 Ford Fusion Hybrid SE
Thanks: 190
Thanked 275 Times in 168 Posts
|
The insurance in the Electric Booger ran out! So it's go time.
Yesterday I started to change the direction of my "new" series wound motor. The first step was brush timing. According to my measurements, this motor has 11-1/2 degree advanced brush timing. You can see the way the brush holder is advanced when compared to the stator pole centre (the longer line):
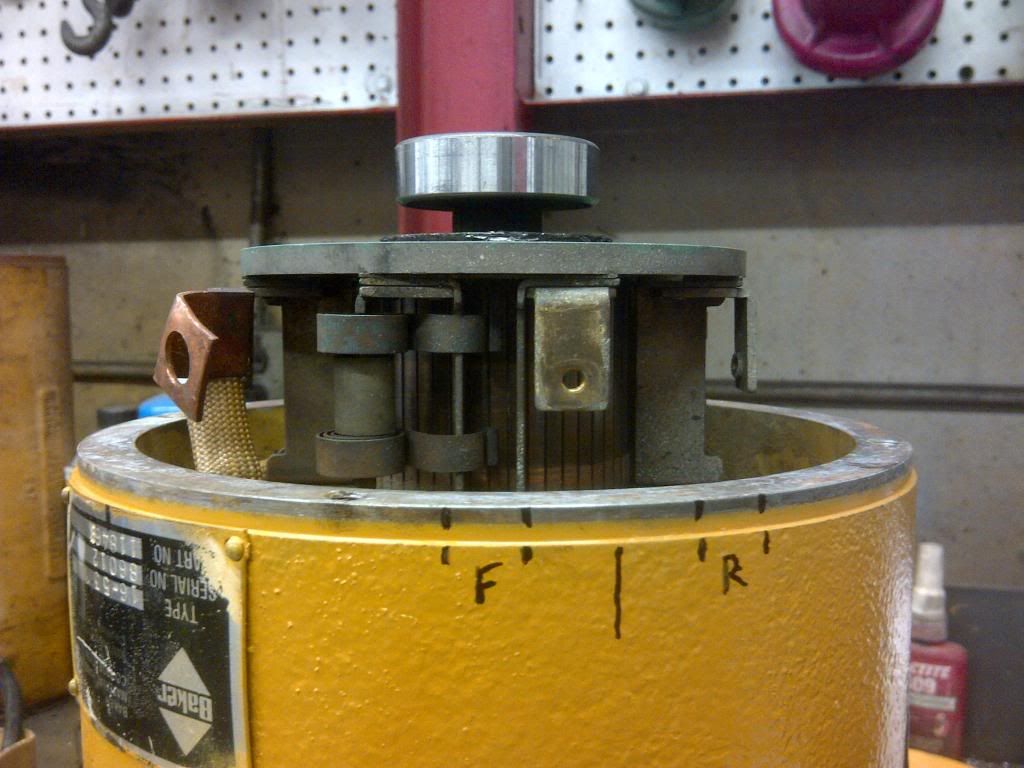
Here is how I want it to be timed for reverse direction:
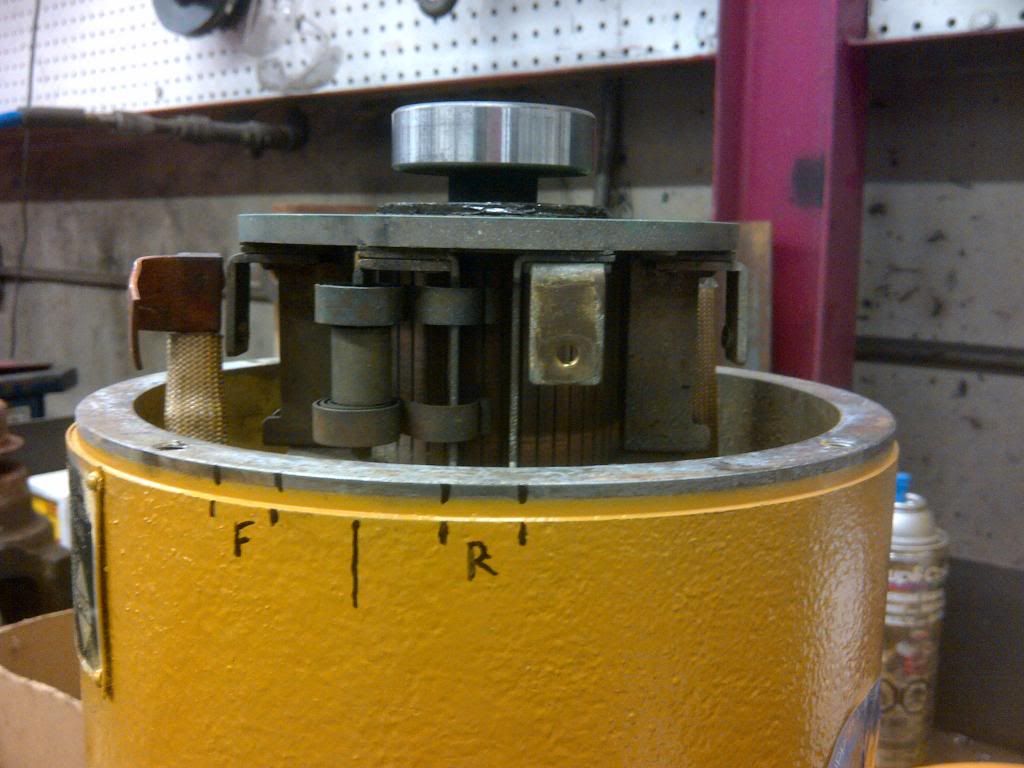
I drilled new holes in the rear cover plate and mounted the brush holder with these new holes. With the end cap installed you can see that I nailed it (probably a fluke):
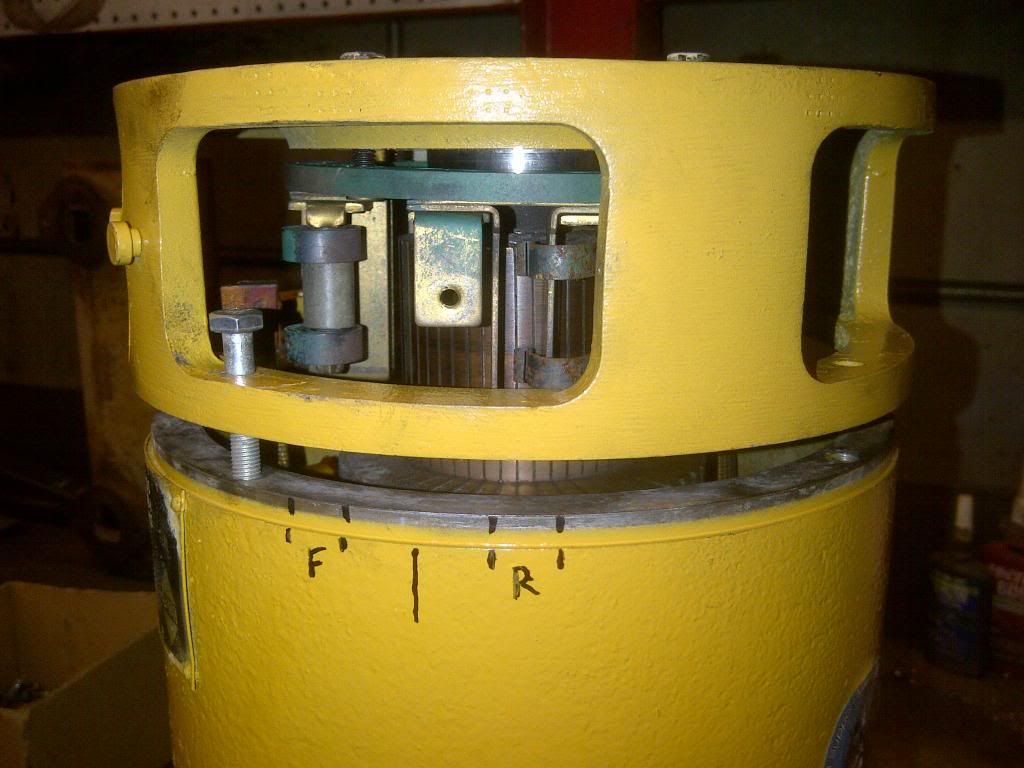
Here you can see the extra holes in the rear cover plate where the brush holder used to mount:
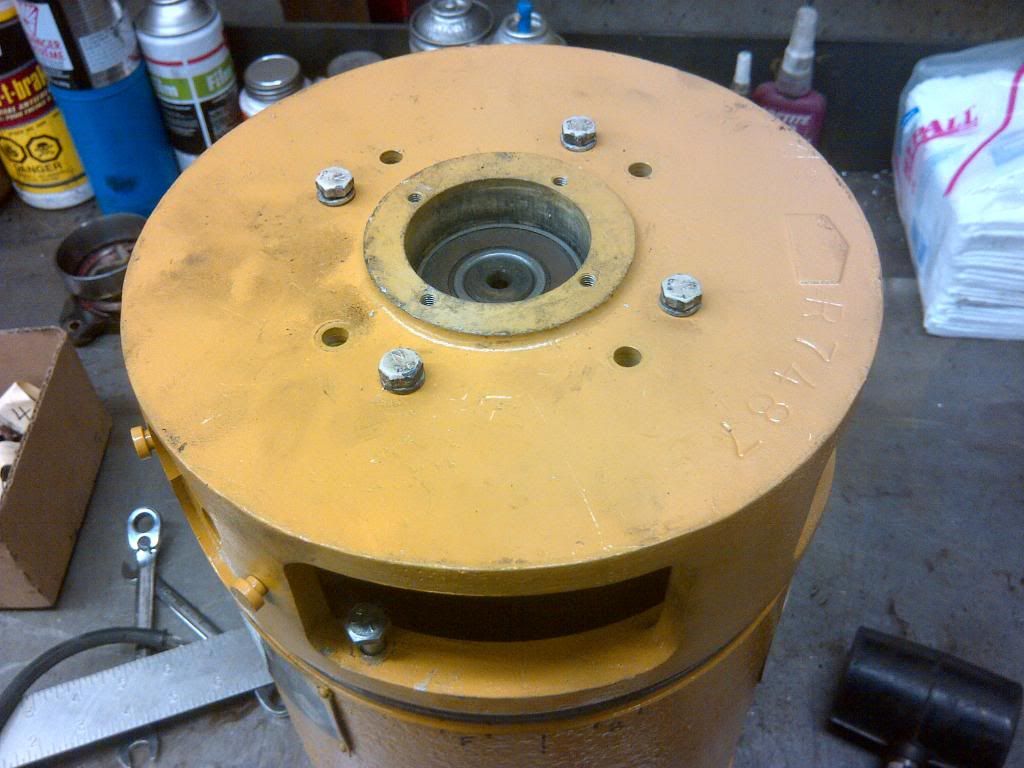
Now I have to rewire the brushes for reverse polarity. This will involve bending one field connection to mate up to a different brush connection, and modifying one brush cable. Hopefully I will have it running backwards very soon. I will probably run the motor at 12V for two hours to make sure the brushes are seated in properly in their new locations.
|
|
|
|